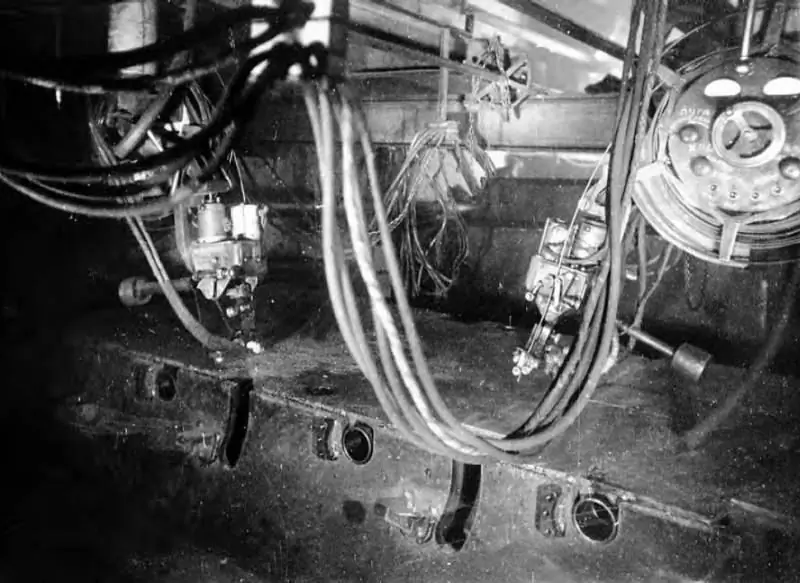
ترويض الدرع
كانت إحدى المشاكل الرئيسية في إنتاج هياكل وأبراج الدبابات المتوسطة T-34 هي التصدع في الأجزاء الملحومة. يتعلق الأمر كله بالصلابة العالية لدرع 8C ، عندما تتشكل تمزقات صغيرة أو شقوق صغيرة بجوار خط اللحام الملحوم. إن وجود الضغوط المتبقية بعد اللحام في المرة الأولى بعد إنتاج السيارة المدرعة لم يكن محسوسًا ، ولكن بمرور الوقت ظهر مع تشققات يصل طولها إلى 500 ملم. كل هذا ، بالطبع ، قلل من مقاومة تأثير دروع الدبابة. لحل هذه المشكلة ، مباشرة بعد تنظيم إنتاج المؤسسات التي تم إجلاؤها ، في النصف الثاني من عام 1942 ، تم جذب متخصصين من معهد المدرعات (TsNII-48) ومعهد اللحام الكهربائي التابع لأكاديمية العلوم في اتحاد الجمهوريات الاشتراكية السوفياتية. تم إجراء البحث في مؤسستين: مصنع أورال تانك رقم 183 في نيجني تاجيل ومصنع أورال للهندسة الثقيلة في سفيردلوفسك. في المجموع ، من يوليو إلى أكتوبر ، قام علماء المعادن وعلماء المواد بالتحقيق في تكوين الشقوق أثناء اللحام لحوالي 9500 قطعة مدرعة. كان الغرض من الدراسة هو العثور على التركيب الكيميائي الأمثل لدرع 8C. اتضح أن أهم عنصر في الدرع في هذه الحالة هو الكربون. إذا كان محتواها في الدرع أكثر من 0.25 ٪ ، فإن صلابة المنطقة المتصلبة في منطقة التماس الملحومة تزداد بشكل حاد ، مما أدى حتماً إلى التشقق.
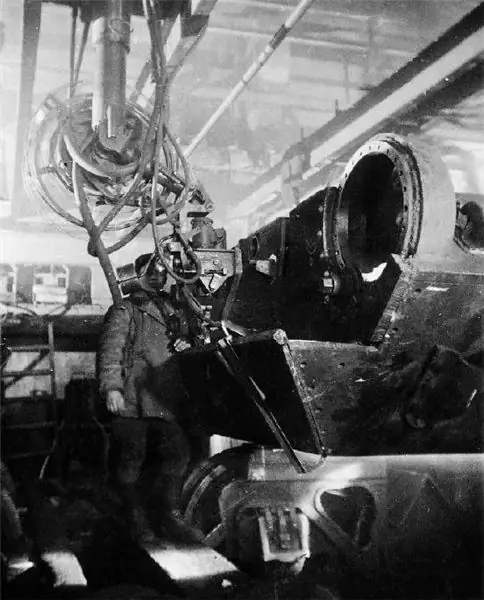
لكن لم يكن من السهل ضمان مثل هذا المحتوى المنخفض من الكربون في الفولاذ المدرع في وقت السلم ، وفي زمن الحرب بدا الأمر مستحيلًا على الإطلاق. أدت التغييرات "التجميلية" الصغيرة في دورة اللحام من خلال استخدام الأقطاب الكهربائية الأوستنيتي ، ونظام متعدد البكرات لتطبيق طبقات اللحام ، والتقسية المنخفضة للتجمعات بعد اللحام إلى زيادة الحد الأعلى لمحتوى الكربون فقط إلى 0.28٪. بالمناسبة ، في صناعة الدبابات الألمانية لم يسمعوا حتى عن مثل هذه المتطلبات الخطيرة لدروع الدبابات - في المتوسط ، كانت حصة الكربون في حدود 0.4-0.5 ٪. كان حل مشكلة ظهور التشققات في منطقة اللحام هو التسخين المسبق للأجزاء إلى 150-200 درجة مئوية ، ثم التبريد البطيء للأجزاء بعد اللحام إلى 100 درجة لمدة 30 دقيقة. لهذا الغرض ، طور معهد Armored محاثات خاصة توفر التسخين المحلي للأجزاء المدرعة في منطقة قطع الغاز أو اللحام. في مصنع Ural Heavy Machine Building Plant ، تم استخدام المحاثات في لحام مفصل الجزء الأمامي بالجوانب والسقف ، وكذلك عند قطع ثقوب الموازنة في الأجزاء الجانبية الصلبة للخزانات. وهكذا ، تم حل مشكلة التصدع أثناء اللحام للفولاذ المدرع متوسط الكربون. بمرور الوقت ، امتدت ممارسة مصنع سفيردلوفسك إلى مصانع الخزانات الأخرى.
آلة لحام
في يوليو 1941 ، بأمر من مجلس مفوضي الشعب ، تم إخلاء معهد اللحام الكهربائي التابع لأكاديمية العلوم في اتحاد الجمهوريات الاشتراكية السوفياتية إلى نيجني تاجيل. لهذا السبب تم تقديم اللحام القوسي المغمور الأوتوماتيكي لهيكل الخزان في Uralvagonzavod لأول مرة. بالطبع ، كانت هذه التكنولوجيا معروفة في وقت سابق ، لكن مجموعة الأكاديمي يفغيني أوسكاروفيتش باتون مع موظفي TsNII-48 كانت قادرة على تكييفها من أجل لحام الفولاذ المدرع. كان فلاديمير إيفانوفيتش دياتلوف أحد العلماء البارزين الذين ساهموا في تطوير اللحام المدرع.قام مع موظفي مصنع خاركوف كومنترن بحل مشكلة تكسير الدرع أثناء اللحام عن طريق إدخال سلك منخفض الكربون في حوض اللحام (المزيد حول هذا أدناه). في عام 1942 ، اكتشف عالم ، وهو الأول من نوعه في العالم ، ظاهرة التنظيم الذاتي لعمليات القوس باستخدام قطب كهربائي قابل للاستهلاك ، مما جعل من الممكن تبسيط تصميم آليات التغذية لآلات اللحام بشكل كبير. أيضًا ، بسبب هذا ، كان من الممكن إنشاء رؤوس لحام أحادية المحرك بسيطة نسبيًا ، وأكثر موثوقية وأرخص. بدون Dyatlov ، لم يكن من الممكن إنشاء تدفقات فعالة تعتمد على خبث أفران الفحم ذات الأفران العالية لمصنع Ashinskiy المعدني ، والتي سميت "تدفقات الخبث ШA". منذ أكتوبر 1943 ، ترأس العالم مختبر اللحام Uralvagonzavod وبقي في هذا المنصب حتى عام 1944 ، حتى تم نقله إلى معهد البحوث المركزي لتقنيات بناء السفن.
لكن بالعودة إلى T-34 الأسطورية ، التي لم تكن لتتحول إلى مثل هذا الدبابة الضخمة ، لولا اللحام الآلي لهيكلها المدرع (الأبراج) في المصانع رقم 183 و UZTM. جعل استخدام آلات اللحام الأوتوماتيكية من الممكن تقليل وقت اللحام بمقدار 3-6.5 مرة. في الوقت نفسه ، تم استخدام ما لا يقل عن 40 مترًا طوليًا من طبقات اللحام لكل فيلق دبابة.
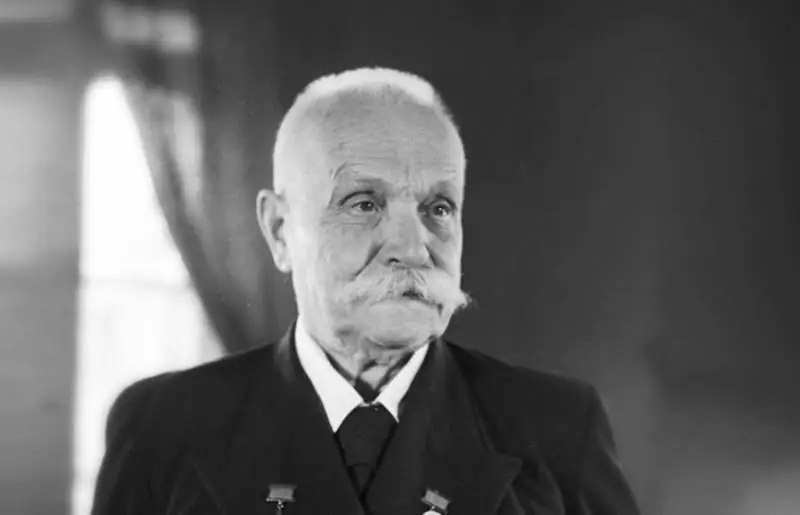
بالإضافة إلى T-34 ، تم استخدام لحام الأكاديمي باتون في مصنع الهيكل المدرع رقم 200 في تشيليابينسك. بمساعدتها ، تم طهي الجزء السفلي من بدن خزان KV ، والذي بلغ إجماليه حوالي 15 مترًا من خط التماس لكل مركبة. من المهم أن أتمتة لحام الدروع جعلت من الممكن جذب العمال ذوي المهارات المنخفضة إلى الإنتاج - كان عمال اللحام الرئيسيون طوال الحرب يعانون من نقص مزمن. منذ يوليو 1942 ، تم تشغيل ناقل خزان فريد من نوعه في نيجني تاجيل ، حيث تم تشغيل 19 وحدة لحام أوتوماتيكية بالقوس المغمور. تقدير حجم الابتكار - أدى ذلك إلى توفير 280 عامل لحام عالي الجودة لأعمال أخرى ، واستبدالهم بـ 57 عاملاً من ذوي المهارات المنخفضة. تحدث الأكاديمي يفغيني أوسكاروفيتش باتون نفسه في مذكرة موجهة إلى سكرتير قسم صناعة الدبابات في اللجنة الإقليمية لسفيردلوفسك للحزب الشيوعي البلشفي لعموم الاتحاد في مارس 1942 عن فعالية إدخال اللحام الآلي (اقتباس من ن. كتاب "صناعة الدبابات في اتحاد الجمهوريات الاشتراكية السوفياتية خلال الحرب الوطنية العظمى"):
"نظرًا للإنتاجية العالية للحام الأوتوماتيكي عالي السرعة تحت طبقات التدفق ، سيتم تقليل وقت اللحام بشكل كبير ، وسيقل استهلاك العمالة والكهرباء وأسلاك الإلكترود."
يمكن العثور على مقارنة بين الوقت المستغرق في اللحام اليدوي والآلي في أرشيف مجمع المعارض في OAO NPK Uralvagonzavod. وفقًا لهم ، يستغرق اللحام ما يزيد قليلاً عن خمس ساعات ، على سبيل المثال ، قطاع من حزام كتف برج T-34 ، ويمكن اللحام التلقائي القيام بذلك في 40 دقيقة فقط. يتم لحام الوصلات السفلية يدويًا في غضون ثلاث ساعات ، وفي الوضع التلقائي - خلال ساعة واحدة.
الكفاح من أجل التماس
لا يمكن القول أن آلات اللحام الأوتوماتيكية ظهرت فجأة في مصانع التجميع في صناعة الخزانات السوفيتية. أولاً ، كانت حصة اللحام اليدوي لا تزال كبيرة جدًا في إنتاج المنتجات المدرعة ، وثانيًا ، في البداية ، لم يكن كل شيء سلسًا مع التكنولوجيا نفسها. لم يكن من الممكن إعطاء اللحام المستوى المطلوب من الليونة - بعد التبريد ، أصبح قاسيًا وهشًا. كان لهذا ، بالطبع ، التأثير الأكثر سلبية على مقاومة مقذوفات الدروع. بعد تحليل الأسباب ، اتضح أن الأمر كله يتعلق بتجاوز عمق الاختراق للمعدن الملحوم ، وخلط السلك المعدني بالمعدن الأساسي وسبائك معدن اللحام بشكل كبير. اقترحت مجموعات من TsNII-48 تحت قيادة I. F Sribny ومن معهد اللحام ، برئاسة V. بادئ ذي بدء ، هذا هو اللحام متعدد المسارات ، عندما تقوم الماكينة بتوصيل الأجزاء المراد لحامها في عدة خطوات.هذا يضمن اختراقًا منخفضًا للمفاصل وتشكيل خط قوي ومرن. من الواضح أن مثل هذه التقنية ليست الأكثر فاعلية في ظروف الحرب: بعد كل شيء ، يتطلب اللحام متعدد المسارات وقتًا طويلاً مقارنةً بالمرور الفردي.
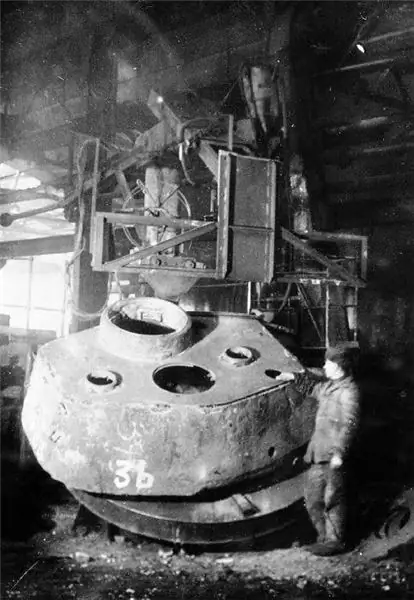
كانت التقنية الثانية من TsNII-48 ومعهد اللحام هي وضع سلك فولاذي منخفض الكربون في أخدود اللحامات لتقليل "تلاشي" المعدن المدرع. نتيجة لذلك ، أصبح التماس بعد التبريد أكثر بلاستيكًا ، وخفض السلك بدرجة كبيرة درجة الحرارة داخل أخدود التماس ، وضاعف أيضًا إنتاجية آلات اللحام. تبين أن هذا هو الأسلوب الأكثر فعالية ، والذي تم تحسينه بشكل أكبر. طريقة جديدة للحام "في سلكين" ، يتم فيها إدخال سلك (حشو) ثانٍ ، غير متصل بالمصدر الحالي ، في حوض اللحام بزاوية سلك القطب. تم حساب تغذية وقطر السلك الثاني بحيث تكون كمية المعدن المودعة منه مساوية لكمية المعدن من سلك القطب المترسب ، أي يجب أن يكون قطر السلك الثاني مساويًا لقطر القطب يجب أن تكون الأسلاك ومعدلات التغذية الخاصة بهم هي نفسها. ومع ذلك ، نظرًا للحاجة إلى إعادة تجهيز الرؤوس الأوتوماتيكية من تغذية سلك واحد إلى تغذية سلكين ، تم تأجيل إدخال هذه الطريقة واستبدالها بالطريقة بإدخال قضيب. ومع ذلك ، في الفترة من يونيو إلى يوليو 1942 ، تم تطبيق هذه الطريقة في المصنع رقم 183 عند لحام مجموعة من الصفائح السفلية لأنف بدن الخزان بعوارض قوسية.
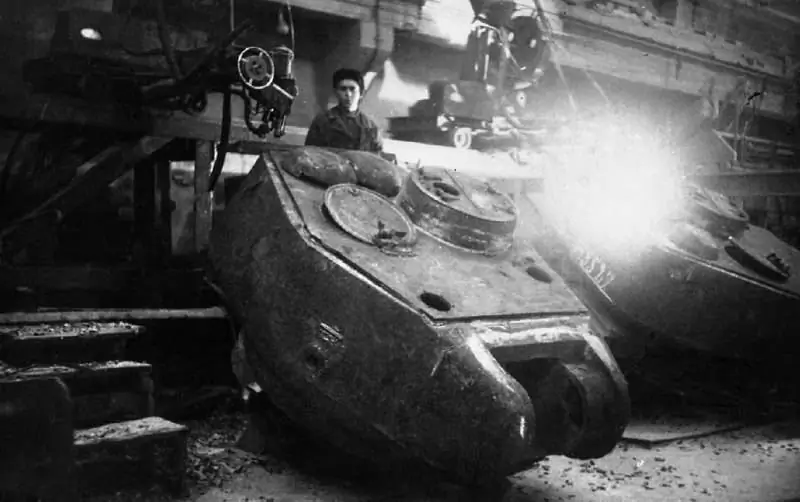
كانت الصعوبات في أتمتة لحام الدبابات (الأبراج) تنظيمية أيضًا. تجدر الإشارة إلى أن آلات اللحام لم يتم تجميعها في سلسلة من قبل وكانت في الواقع منتجات الإنتاج التجريبي لمعهد اللحام. وهذا ما يفسر بعض البطء في تطوير تقنيات جديدة في صناعة الخزانات. لذلك ، بحلول نهاية عام 1942 ، كان لدى مصانع الخزانات 30 إلى 35 آلة لحام فقط ، والتي ، بالطبع ، لم تكن كافية. لذلك ، أمر مفوض الشعب IM Zaltsman ، بأمر رقم 200 بتاريخ 28 مارس 1943 ، في المصنع رقم 183 بتركيب 7 وحدات لحام آلي إضافية بحلول منتصف مايو ، في مصنع Ural Heavy Machine Building Plant بحلول 1 يونيو ، 8 آلات أوتوماتيكية وبحلول 15 يونيو ، طلبت 5 وحدات تسليمها إلى مصنع تشيليابينسك.رقم 200. كانت هذه الخطوة واحدة من العديد من الخطوات التي سمحت لصناعة الدبابات المحلية بالوصول إلى أهداف الإنتاج المخطط لها للمركبات المدرعة المتعقبة التي تشتد الحاجة إليها في المقدمة.