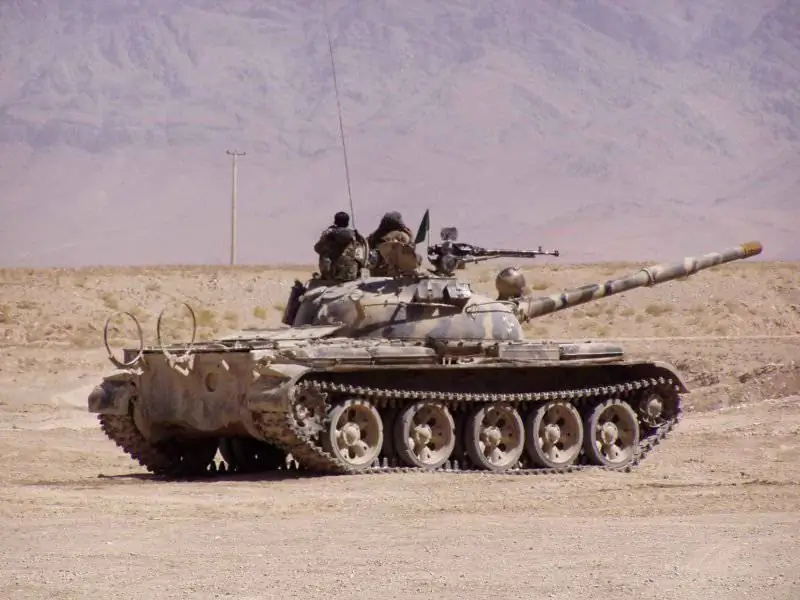
في عام 1955 ، تم اتخاذ قرار حكومي لإنشاء مكتب تصميم لهندسة الديزل الخاصة في مصنع خاركوف لهندسة النقل وإنشاء محرك ديزل جديد للخزان. تم تعيين البروفيسور أ.د. شارومسكي كبير المصممين لمكتب التصميم.

تم تحديد اختيار مخطط تصميم محرك الديزل المستقبلي بشكل أساسي من خلال تجربة العمل على محركات الديزل ثنائية الأشواط OND TsIAM ومحرك U-305 ، بالإضافة إلى الرغبة في تلبية متطلبات مصممي محرك T الجديد. -64 دبابة تم تطويرها في هذا المصنع تحت قيادة كبير المصممين AA … موروزوف: لضمان الحد الأدنى من أبعاد محرك الديزل ، خاصة في الارتفاع ، مع إمكانية وضعه في الخزان في وضع عرضي بين علب التروس الكوكبية الموجودة على متن الطائرة. تم اختيار مخطط ديزل ثنائي الأشواط بترتيب أفقي مكون من خمس أسطوانات مع تحريك المكابس بشكل معاكس فيها. تقرر صنع محرك به تضخم واستخدام طاقة غاز العادم في التوربينات.
ما هو الأساس المنطقي وراء اختيار محرك ديزل ثنائي الأشواط؟
في وقت سابق ، في عشرينيات وثلاثينيات القرن الماضي ، تم تأجيل إنشاء محرك ديزل ثنائي الأشواط لمركبات الطيران والمركبات الأرضية بسبب العديد من المشكلات التي لم يتم حلها والتي لا يمكن التغلب عليها بمستوى المعرفة والخبرة والقدرات للصناعة المحلية التي تراكمت من قبل هذا الوقت.
أدت دراسة وأبحاث محركات الديزل ثنائية الأشواط لبعض الشركات الأجنبية إلى استنتاج حول الصعوبة الكبيرة في إتقانها في الإنتاج. لذلك ، على سبيل المثال ، أظهرت دراسة أجراها المعهد المركزي لمحركات الطيران (CIAM) في الثلاثينيات لمحرك الديزل Jumo-4 الذي صممه Hugo Juneckers مشاكل كبيرة مرتبطة بتطوير مثل هذه المحركات في إنتاج مثل هذه المحركات من قبل الشركات المحلية. صناعة تلك الفترة. كان معروفًا أيضًا أن إنجلترا واليابان ، بعد أن اشتريتا ترخيصًا لمحرك الديزل هذا ، عانتا من إخفاقات في تطوير محرك Junkers. في الوقت نفسه ، في الثلاثينيات والأربعينيات من القرن الماضي ، تم بالفعل إجراء أعمال بحثية على محركات الديزل ثنائية الأشواط في بلدنا وتم تصنيع عينات تجريبية من هذه المحركات. يعود الدور الرائد في هذه الأعمال إلى متخصصي CIAM ، وعلى وجه الخصوص ، إلى قسم محركات النفط (OND). تم تصميم وتصنيع عينات من محركات الديزل ثنائية الأشواط من CIAM: OH-2 (12/16 ، 3) ، OH-16 (11/14) ، OH-17 (18/20) ، OH-4 (8 / 9) وعدد من المحركات الأصلية الأخرى.
من بينها محرك FED-8 ، المصمم بتوجيه من علماء المحركات البارزين BS Stechkin ، N. R. Briling ، A. A. Bessonov. كان محرك ديزل للطائرات ثنائي الأشواط ذو 16 أسطوانة على شكل X مع توزيع غاز مكبس الصمام ، بأبعاد 18/23 ، يولد قوة 1470 كيلوواط (2000 حصان). أحد ممثلي محركات الديزل ثنائية الأشواط مع الشحن الفائق هو محرك ديزل توربو بست أسطوانات على شكل نجمة بسعة 147 … 220 كيلو واط (200 … 300 حصان) تم تصنيعه في CIAM تحت قيادة BS Stechkin. تم نقل قوة التوربينات الغازية إلى العمود المرفقي من خلال علبة تروس مناسبة.
يمثل القرار الذي تم اتخاذه عند إنشاء محرك FED-8 من حيث الفكرة نفسها ومخطط التصميم خطوة مهمة إلى الأمام. ومع ذلك ، فإن عملية التشغيل وخاصة عملية تبادل الغازات عند درجة عالية من الضغط ونفخ الحلقة لم يتم إجراؤها بشكل مبدئي.لذلك ، لم يتلق ديزل FED-8 مزيدًا من التطوير وفي عام 1937 توقف العمل عليه.
بعد الحرب ، أصبحت الوثائق الفنية الألمانية ملكًا لاتحاد الجمهوريات الاشتراكية السوفياتية. سقطت في م. Charomsky كمطور لمحركات الطائرات ، وهو مهتم بحقيبة Junkers.
حقيبة سفر Junkers - سلسلة من محركات الطائرات ذات الشوطين التوربيني التوربيني Jumo 205 مع مكابس متحركة معاكسة تم إنشاؤها في أوائل الثلاثينيات من القرن العشرين. خصائص محرك Jumo 205-C كالتالي: 6 أسطوانات ، 600 حصان. السكتة الدماغية 2 × 160 مم ، الإزاحة 16.62 لترًا ، نسبة الضغط 17: 1 ، عند 2200 دورة في الدقيقة
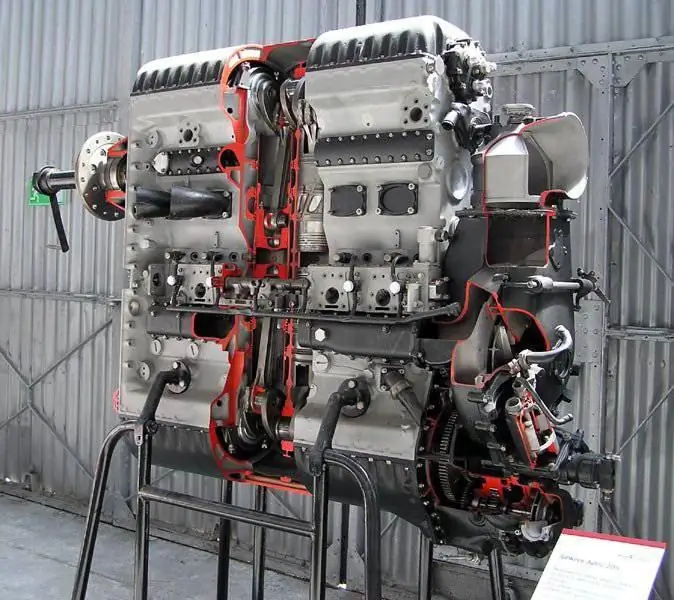
محرك جومو 205
خلال الحرب ، تم إنتاج حوالي 900 محرك ، والتي تم استخدامها بنجاح في الطائرات المائية Do-18 و Do-27 ، وفيما بعد على القوارب عالية السرعة. بعد فترة وجيزة من نهاية الحرب العالمية الثانية في عام 1949 ، تقرر تركيب هذه المحركات على زوارق الدورية في ألمانيا الشرقية ، والتي كانت في الخدمة حتى الستينيات.
على أساس هذه التطورات ، ابتكرت AD Charomsky في عام 1947 في اتحاد الجمهوريات الاشتراكية السوفياتية محرك ديزل ثنائي الأشواط M-305 ومقصورة أحادية الأسطوانة لمحرك U-305. طور محرك الديزل هذا قوة 7350 كيلو واط (10000 حصان) مع وزن محدد منخفض (0 ، 5 كجم / ساعة) واستهلاك منخفض للوقود النوعي -190 جم / كيلو وات ساعة (140 جم / ساعة). تم اعتماد ترتيب على شكل X يتكون من 28 أسطوانة (أربع كتل من 7 أسطوانات). تم اختيار أبعاد المحرك التي تساوي 12/12. تم توفير دفعة عالية بواسطة شاحن توربيني متصل ميكانيكيًا بعمود الديزل. للتحقق من الخصائص الرئيسية المنصوص عليها في مشروع M-305 ، للعمل على عملية العمل وتصميم الأجزاء ، تم بناء نموذج تجريبي للمحرك ، والذي يحتوي على مؤشر U-305. أورلوفا ، ني روداكوف ، إل في أوستينوفا ، إن إس زولوتاريف ، إس إم شيفرين ، إن إس سوبوليف ، بالإضافة إلى التقنيين والعاملين في المصنع التجريبي لـ CIAM وورشة عمل OND.
لم يتم تنفيذ مشروع ديزل الطائرة بالحجم الكامل M-305 ، حيث أن عمل CIAM ، مثل صناعة الطيران بأكملها في البلاد ، في ذلك الوقت كان يركز بالفعل على تطوير المحركات التوربينية والتوربينية والحاجة إلى اختفى محرك ديزل بقوة 10000 حصان للطيران.
المؤشرات العالية التي تم الحصول عليها على محرك الديزل U-305: قوة محرك اللتر 99 كيلو واط / لتر (135 حصان / لتر) ، وقوة اللتر من أسطوانة واحدة تبلغ 220 كيلو واط (300 حصان) عند ضغط زيادة 0.35 ميجا باسكال ؛ سرعة دوران عالية (3500 دورة في الدقيقة) وبيانات من عدد من الاختبارات الناجحة طويلة المدى للمحرك - أكدت إمكانية إنشاء محرك ديزل فعال صغير الحجم ثنائي الأشواط لأغراض النقل بمؤشرات وعناصر هيكلية مماثلة.
في عام 1952 ، تم تحويل المختبر رقم 7 (OND سابقًا) التابع لـ CIAM بقرار حكومي إلى مختبر أبحاث المحركات (NILD) مع خضوعه لوزارة هندسة النقل. مجموعة مبادرة من الموظفين - متخصصون ذوو مؤهلات عالية في محركات الديزل (G. V. Orlova ، NI Rudakov ، S. M. Shifrin ، إلخ) ، برئاسة الأستاذ A. D. Charomsky ، موجودون بالفعل في NILD (لاحقًا - NIID). محرك U-305 ثنائي الشوط.
ديزل 5TDF
في عام 1954 ، قدم A. D. Charomsky اقتراحًا إلى الحكومة لإنشاء محرك ديزل بخزان ثنائي الأشواط. تزامن هذا الاقتراح مع متطلبات المصمم الرئيسي للخزان الجديد A. A. موروزوف ، وأ. تم تعيين شارومسكي كبير المصممين للمصنع. V. ماليشيف في خاركوف.
نظرًا لأن مكتب تصميم محرك الخزان لهذا المصنع ظل في الغالب في تشيليابينسك ، م. كان على Charomsky تشكيل مكتب تصميم جديد ، وإنشاء قاعدة تجريبية ، وإنشاء إنتاج تجريبي ومتسلسل ، وتطوير تقنية لم يكن لدى المصنع. بدأ العمل في تصنيع وحدة أحادية الأسطوانة (OTsU) ، على غرار محرك U-305. في OTsU ، تم العمل على عناصر وعمليات محرك الديزل ذي الخزان الكامل الحجم المستقبلي.
كان المشاركون الرئيسيون في هذا العمل هم A. D. Charomsky ، و GA Volkov ، و L. L. Golinets ، و B. M. Kugel ، و MA ، و Meksin ، و I. L. Rovensky ، وغيرهم.
في عام 1955 ، انضم موظفو NILD إلى أعمال التصميم في مصنع الديزل: قام كل من G. V. Orlova ، NI Rudakov ، VG Lavrov ، I. S. Elperin ، I. K. Lagovsky وغيرهم من المتخصصين في NILD L. في OTsU في مصنع هندسة النقل في خاركوف. هكذا يظهر 4TPD السوفيتي.لقد كان محركًا يعمل ، ولكن مع وجود عيب واحد - كانت القوة تزيد قليلاً عن 400 حصان ، وهو ما لم يكن كافياً لخزان. تضع Charomsky أسطوانة أخرى وتحصل على 5TD.
أدى إدخال أسطوانة إضافية إلى تغيير ديناميكيات المحرك بشكل خطير. نشأ عدم توازن تسبب في حدوث اهتزازات التوائية شديدة في النظام. تشارك القوى العلمية الرائدة في لينينغراد (VNII-100) وموسكو (NIID) وخاركوف (KhPI) في حلها. تم إحضار 5TDF إلى الحالة بشكل تجريبي ، عن طريق التجربة والخطأ.
تم اختيار أبعاد هذا المحرك بما يعادل 12/12 ، أي كما هو الحال في محرك U-305 و OTsU. لتحسين استجابة دواسة الوقود لمحرك الديزل ، تقرر توصيل التوربين والضاغط ميكانيكياً بالعمود المرفقي.
يحتوي الديزل 5TD على الميزات التالية:
- قوة عالية - 426 كيلو واط (580 حصان) بأبعاد كلية صغيرة نسبيًا ؛
- زيادة السرعة - 3000 دورة في الدقيقة ؛
- كفاءة الضغط والاستفادة من طاقة الغازات العادمة ؛
- ارتفاع منخفض (أقل من 700 مم) ؛
- انخفاض بنسبة 30-35٪ في نقل الحرارة مقارنة بمحركات الديزل الحالية رباعية الأشواط (التي تُستنشق بشكل طبيعي) ، وبالتالي ، حجم أصغر مطلوب لنظام التبريد في محطة توليد الكهرباء ؛
- كفاءة وقود مرضية والقدرة على تشغيل المحرك ليس فقط على وقود الديزل ، ولكن أيضًا على الكيروسين والبنزين وخلائطهما المختلفة ؛
- مأخذ الطاقة من طرفيه وطوله الصغير نسبيًا ، مما يجعل من الممكن تجميع خزان MTO بترتيب عرضي لمحرك ديزل بين علبتي تروس على متن السيارة في حجم مشغول أصغر بكثير من الترتيب الطولي لـ المحرك وعلبة التروس المركزية.
- التنسيب الناجح لوحدات مثل ضاغط الهواء عالي الضغط بأنظمته الخاصة ، ومولد بدء التشغيل ، وما إلى ذلك.
بعد أن احتفظ المصممون بالترتيب العرضي للمحرك بإقلاع طاقة ثنائي الاتجاه وناقل حركة كوكبيان على متن الطائرة يقعان على جانبي المحرك ، انتقل المصممون إلى الأماكن الشاغرة على جانبي المحرك ، بالتوازي مع علب التروس ، الضاغط والتوربينات الغازية ، تم تركيبهما مسبقًا في 4TD أعلى كتلة المحرك. أتاح التصميم الجديد خفض حجم MTO إلى النصف مقارنةً بخزان T-54 ، وتم استبعاد المكونات التقليدية مثل علبة التروس المركزية وعلبة التروس والقابض الرئيسي وآليات التأرجح الكوكبية على متن الطائرة والمحركات النهائية والفرامل. كما لوحظ لاحقًا في تقرير GBTU ، وفر النوع الجديد من ناقل الحركة 750 كجم من الكتلة ويتألف من 150 قطعة آلية بدلاً من 500 السابقة.
تم تعشيق جميع أنظمة خدمة المحرك فوق محرك الديزل ، لتشكيل "الطابق الثاني" من MTO ، والذي سمي مخططه "بمستويين".
تطلب الأداء العالي لمحرك 5TD استخدام عدد من الحلول الأساسية الجديدة والمواد الخاصة في تصميمه. مكبس هذا الديزل ، على سبيل المثال ، تم تصنيعه باستخدام وسادة حرارية ومباعد.
كانت حلقة المكبس الأولى عبارة عن حلقة لهب مستمرة من نوع الشفة. كانت الاسطوانات مصنوعة من الفولاذ المطلي بالكروم.
تم توفير القدرة على تشغيل المحرك بضغط فلاش عالٍ من خلال دائرة الطاقة للمحرك مع مسامير فولاذية داعمة ، وكتلة من الألومنيوم المصبوب يتم تفريغها من تأثير قوى الغاز ، وعدم وجود وصلة غاز. تم تسهيل تحسين عملية تطهير وتعبئة الأسطوانات (وهذه مشكلة لجميع محركات الديزل ثنائية الشوط) إلى حد ما من خلال مخطط الغاز الديناميكي باستخدام الطاقة الحركية لغازات العادم وتأثير الطرد.
يضمن نظام تكوين خليط الدوامة النفاثة ، الذي يتم فيه تنسيق طبيعة واتجاه نفاثات الوقود مع اتجاه حركة الهواء ، حدوث اضطراب فعال لخليط الوقود والهواء ، مما ساهم في تحسين عملية نقل الحرارة والكتلة.
كما أتاح الشكل المختار خصيصًا لغرفة الاحتراق إمكانية تحسين عملية الخلط والاحتراق.تم سحب أغطية المحمل الرئيسية مع علبة المرافق بواسطة براغي طاقة فولاذية ، مع أخذ الحمل من قوى الغاز التي تعمل على المكبس.
تم إرفاق صفيحة مع توربين ومضخة مياه بأحد طرفي كتلة علبة المرافق ، وتم توصيل لوحة ناقل الحركة الرئيسي والأغطية بمحركات إلى الشاحن التوربيني والمنظم ومستشعر سرعة الدوران وضاغط الضغط العالي وموزع الهواء في الجهة المقابلة. نهاية.
في يناير 1957 ، تم إعداد أول نموذج أولي لمحرك الديزل 5TD لاختبارات مقاعد البدلاء. في نهاية اختبارات مقاعد البدلاء ، تم نقل 5TD في نفس العام لتجارب الكائنات (البحرية) في خزان تجريبي "Object 430" ، وبحلول مايو 1958 اجتازت اختبارات الحالة بين الأقسام بعلامة جيدة.
ومع ذلك ، فقد تقرر عدم نقل الديزل 5TD إلى الإنتاج الضخم. كان السبب مرة أخرى هو التغيير في متطلبات الجيش للدبابات الجديدة ، الأمر الذي استلزم مرة أخرى زيادة في القوة. مع الأخذ في الاعتبار المؤشرات الفنية والاقتصادية العالية جدًا لمحرك 5TD والاحتياطيات الكامنة فيه (والتي تم إثباتها أيضًا من خلال الاختبارات) ، محطة طاقة جديدة بسعة حوالي 700 حصان. قررت أن تخلق على أساسها.
يتطلب إنشاء مثل هذا المحرك الأصلي لمصنع خاركوف لهندسة النقل تصنيع معدات تكنولوجية مهمة وعدد كبير من النماذج الأولية لمحرك ديزل واختبارات متكررة طويلة المدى. يجب أن يؤخذ في الاعتبار أن قسم التصميم في المصنع أصبح فيما بعد مكتب تصميم خاركوف للهندسة الميكانيكية (KHKBD) ، وتم إنشاء إنتاج المحركات عمليًا من الصفر بعد الحرب.
بالتزامن مع تصميم محرك الديزل ، تم إنشاء مجمع كبير من المدرجات التجريبية وتركيبات مختلفة (24 وحدة) في المصنع لاختبار عناصر تصميمه وسير العمل. ساعد هذا بشكل كبير في التحقق من تصميمات وحدات مثل الشاحن الفائق ، والتوربينات ، ومضخة الوقود ، ومشعب العادم ، والطرد المركزي ، ومضخات المياه والنفط ، وعلبة المرافق ، وما إلى ذلك ، واستمر تطويرها بشكل كبير.
في عام 1959 ، بناءً على طلب كبير المصممين للخزان الجديد (AA Morozov) ، الذي تم تصميم محرك الديزل هذا من أجله ، كان من الضروري زيادة قوته من 426 كيلو واط (580 حصان) إلى 515 كيلو واط (700) حصان).). تم تسمية الإصدار القسري للمحرك باسم 5TDF.
من خلال زيادة سرعة ضاغط التعزيز ، تمت زيادة قوة اللتر للمحرك. ومع ذلك ، نتيجة لإجبار محرك الديزل ، ظهرت مشاكل جديدة ، في المقام الأول في موثوقية المكونات والتجمعات.
قام مصممو KhKBD و NIID و VNIITransmash وتقنيو المصنع والمعاهد VNITI و TsNITI (منذ عام 1965) بإجراء قدر كبير من العمليات الحسابية والبحث والتصميم والعمل التكنولوجي لتحقيق الموثوقية المطلوبة ووقت التشغيل لمحرك الديزل 5TDF.
كانت أصعب المشاكل هي مشاكل زيادة موثوقية مجموعة المكبس ، ومعدات الوقود ، والشاحن التوربيني. تم تقديم كل تحسين ، حتى وإن كان ضئيلًا ، كنتيجة لمجموعة كاملة من تدابير التصميم والتقنية والتنظيمية (الإنتاج).
تميزت الدفعة الأولى من محركات الديزل 5TDF بعدم الاستقرار الكبير في جودة الأجزاء والتجمعات. تراكمت مدة تشغيل الضمان المحددة في جزء معين من محركات الديزل من السلسلة المنتجة (الدُفعة) (300 ساعة). في الوقت نفسه ، تمت إزالة جزء كبير من المحركات من المدرجات قبل فترة الضمان بسبب بعض العيوب.
تكمن خصوصية محرك الديزل عالي السرعة ثنائي الأشواط في نظام تبادل غازات أكثر تعقيدًا مما هو عليه في 4 أشواط ، وزيادة استهلاك الهواء ، وزيادة الحمل الحراري لمجموعة المكبس.لذلك ، صلابة الهيكل ومقاومة الاهتزازات ، والمراعاة الأكثر صرامة للشكل الهندسي لعدد من الأجزاء ، وخصائص عالية ضد الاستيلاء ومقاومة التآكل للأسطوانات ، ومقاومة الحرارة والقوة الميكانيكية للمكابس ، وإمداد الجرعات الدقيقة وإزالة زيوت التشحيم و كانت هناك حاجة إلى تحسين جودة أسطح الاحتكاك. لمراعاة هذه الميزات المحددة للمحركات ثنائية الشوط ، كان من الضروري حل مشاكل التصميم والتكنولوجيا المعقدة.
أحد الأجزاء الأكثر أهمية التي توفر توزيعًا دقيقًا للغاز وحماية حلقات إحكام الغلق للمكبس من ارتفاع درجة الحرارة كانت حلقة اللهب ذات الجدران الرقيقة المصنوعة من الصلب الملولب والمزودة بطبقة خاصة مضادة للاحتكاك. في تحسين محرك الديزل 5TDF ، أصبحت مشكلة قابلية تشغيل هذه الحلقة واحدة من المشكلات الرئيسية. في عملية الضبط الدقيق ، حدث جرجر وكسر في حلقات اللهب لفترة طويلة بسبب تشوه مستوى دعمها ، والتكوين دون الأمثل لكل من الحلقة نفسها وجسم المكبس ، وطلاء الكروم غير المرضي للحلقات ، وعدم كفاية التشحيم ، إمداد الوقود غير المتكافئ عن طريق الفوهات ، وتقطيع الحجم وترسب الأملاح المتكونة على بطانة المكبس ، وكذلك بسبب تآكل الغبار المرتبط بدرجة غير كافية لتنظيف الهواء الذي يسحبه المحرك.
فقط نتيجة العمل الطويل والشاق للعديد من المتخصصين في المصنع والمعاهد البحثية والتكنولوجية ، حيث تم تحسين تكوين المكبس وحلقة اللهب ، وتحسين تكنولوجيا التصنيع ، وتحسين عناصر معدات الوقود ، تم تحسين التشحيم ، وتم التخلص عمليًا من استخدام الطلاءات المضادة للاحتكاك الأكثر فعالية ، فضلاً عن تحسين عيوب نظام تنظيف الهواء المرتبطة بتشغيل حلقة اللهب.
تم التخلص من أعطال حلقات المكبس شبه المنحرفة ، على سبيل المثال ، عن طريق تقليل الخلوص المحوري بين الحلقة وأخدود المكبس ، وتحسين المواد ، وتغيير تكوين المقطع العرضي للحلقة (التبديل من شبه منحرف إلى مستطيل) وصقل التقنية لتصنيع الحلقات. تم إصلاح كسور براغي بطانة المكبس عن طريق إعادة الخيوط والقفل ، وتشديد ضوابط التصنيع ، وتشديد حدود عزم الدوران ، واستخدام مادة مسامير محسّنة.
تم تحقيق استقرار استهلاك الزيت عن طريق زيادة صلابة الأسطوانات ، وتقليل حجم القواطع في نهايات الأسطوانات ، وتشديد التحكم في تصنيع حلقات تجميع الزيت.
من خلال الضبط الدقيق لعناصر معدات الوقود وتحسين تبادل الغازات ، تم الحصول على بعض التحسن في كفاءة الوقود وانخفاض في الحد الأقصى لضغط الفلاش.
من خلال تحسين جودة المطاط المستخدم وتبسيط الفجوة بين الأسطوانة والكتلة ، تم القضاء على حالات تسرب سائل التبريد عبر حلقات الختم المطاطية.
فيما يتعلق بالزيادة الكبيرة في نسبة التروس من العمود المرفقي إلى الشحان الفائق ، كشفت بعض محركات الديزل 5TDF عن عيوب مثل الانزلاق والتآكل في أقراص القابض الاحتكاكية ، وانهيار عجلة الشاحن ، وفشل محاملها ، والتي كانت غائبة عن المحرك. محرك ديزل 5TD. للتخلص منها ، كان من الضروري تنفيذ إجراءات مثل اختيار الشد الأمثل لحزمة قرص القابض الاحتكاك ، وزيادة عدد الأقراص في العبوة ، والقضاء على مكثفات الضغط في دافع الشاحن التوربيني الفائق ، واهتزاز العجلة ، وزيادة خصائص التخميد الدعم واختيار محامل أفضل. هذا جعل من الممكن القضاء على العيوب الناتجة عن إجبار محرك الديزل من حيث القوة.
ساهمت الزيادة في الموثوقية ووقت التشغيل لمحرك الديزل 5TDF بشكل كبير في استخدام زيوت عالية الجودة مع إضافات خاصة.
في منصات VNIITransmash ، بمشاركة موظفي KKBD و NIID ، تم إجراء قدر كبير من الأبحاث حول تشغيل محرك الديزل 5TDF في ظروف الغبار الحقيقي للهواء الداخل. وقد توجت في النهاية باختبار "الغبار" الناجح للمحرك على مدى 500 ساعة من التشغيل.أكد هذا الدرجة العالية من التطور لمجموعة أسطوانات المكبس لمحرك الديزل ونظام تنقية الهواء.
بالتوازي مع الضبط الدقيق للديزل نفسه ، تم اختباره مرارًا وتكرارًا بالاشتراك مع أنظمة محطة الطاقة. في الوقت نفسه ، تم تحسين الأنظمة ، وتم حل مشكلة الترابط والتشغيل الموثوق به في الخزان.
كانت L. L. Golinets هي المصمم الرئيسي لـ KHKBD في الفترة الحاسمة لضبط محرك الديزل 5TDF. تقاعد كبير المصممين السابق أ.د. تشارومسكي واستمر في المشاركة في الصقل كمستشار.
تسبب تطوير الإنتاج التسلسلي لمحرك الديزل 5TDF في ورش العمل الجديدة المصممة لهذا الغرض في المصنع ، مع كوادر جديدة من العمال والمهندسين الذين درسوا على هذا المحرك ، في العديد من الصعوبات ، بمشاركة متخصصين من منظمات أخرى.
حتى عام 1965 ، تم إنتاج محرك 5TDF في سلسلة منفصلة (دفعات). تضمنت كل سلسلة لاحقة عددًا من الإجراءات التي تم تطويرها واختبارها في المدرجات ، مما أدى إلى القضاء على العيوب التي تم تحديدها أثناء الاختبار وأثناء العملية التجريبية في الجيش.
ومع ذلك ، فإن وقت التشغيل الفعلي للمحركات لم يتجاوز 100 ساعة.
حدث تقدم كبير في تحسين موثوقية الديزل في بداية عام 1965. بحلول هذا الوقت ، تم إجراء قدر كبير من التغييرات على تصميم وتكنولوجيا تصنيعها. أدخلت هذه التغييرات في الإنتاج ، وجعلت من الممكن زيادة وقت تشغيل السلسلة التالية من المحركات حتى 300 ساعة. أكدت اختبارات التشغيل طويلة المدى للخزانات المزودة بمحركات من هذه السلسلة زيادة موثوقية محركات الديزل بشكل كبير: عملت جميع المحركات خلال هذه الاختبارات 300 ساعة ، وعمل بعضها (بشكل انتقائي) ، مع استمرار الاختبارات ، 400 … 500 ساعة لكل منهما.
في عام 1965 ، تم إطلاق مجموعة تركيب من محركات الديزل أخيرًا وفقًا لتوثيق الرسم الفني المصحح وتقنية الإنتاج الضخم. تم تصنيع ما مجموعه 200 محرك تسلسلي في عام 1965. بدأ تكثيف الإنتاج وبلغ ذروته في عام 1980. في سبتمبر 1966 ، اجتاز محرك الديزل 5TDF اختبارات بين الأقسام.
بالنظر إلى تاريخ إنشاء محرك الديزل 5TDF ، تجدر الإشارة إلى التقدم في تطوره التكنولوجي كمحرك جديد تمامًا لإنتاج المصنع. في وقت واحد تقريبًا مع تصنيع النماذج الأولية للمحرك وصقل تصميمه ، تم تنفيذ تطويره التكنولوجي وإنشاء مرافق إنتاج جديدة للمصنع واستكمالها بالمعدات.
وفقًا للرسومات المنقحة لعينات المحرك الأولى ، في عام 1960 بالفعل ، بدأ تطوير تقنية التصميم لتصنيع 5TDF ، وفي عام 1961 ، بدأ إنتاج وثائق تقنية العمل. تتطلب ميزات تصميم محرك ديزل ثنائي الشوط ، واستخدام مواد جديدة ، والدقة العالية لفرده ومكوناته ، التكنولوجيا لاستخدام طرق جديدة بشكل أساسي في معالجة المحرك وحتى تجميعه. تم تنفيذ تصميم العمليات التكنولوجية ومعداتها من قبل الخدمات التكنولوجية للمصنع ، برئاسة A. I. Isaev و V. D. Dyachenko و V. I. Doschechkin وآخرون ، ومن قبل موظفي المعاهد التكنولوجية للصناعة. شارك متخصصون من المعهد المركزي لبحوث المواد (مدير FA Kupriyanov) في حل العديد من مشاكل علم المعادن والمواد.
تم تنفيذ إنشاء متاجر جديدة لإنتاج السيارات في مصنع خاركوف لهندسة النقل وفقًا لمشروع معهد Soyuzmashproekt (كبير مهندسي المشروع S. I. Shpynov).
خلال الفترة 1964-1967. تم الانتهاء من إنتاج الديزل الجديد بالمعدات (خاصة الآلات الخاصة - أكثر من 100 وحدة) ، والتي بدونها سيكون من المستحيل عمليًا تنظيم الإنتاج التسلسلي لأجزاء الديزل. كانت هذه آلات حفر الماس ومتعددة المغازل لمعالجة الكتل ، وآلات الخراطة والتشطيب الخاصة لمعالجة أعمدة الكرنك ، إلخ.قبل بدء ورش العمل الجديدة ومناطق الاختبار وتصحيح تكنولوجيا التصنيع لعدد من الأجزاء الرئيسية ، بالإضافة إلى تصنيع مجموعات التركيب والسلسلة الأولى من المحرك ، تم تنظيم هياكل قاطرات الديزل الكبيرة مؤقتًا عند الإنتاج المواقع.
تم تنفيذ السعات الرئيسية لإنتاج الديزل الجديد بالتناوب في الفترة 1964-1967. في ورش العمل الجديدة ، تم توفير دورة كاملة من إنتاج الديزل 5TDF ، باستثناء الإنتاج الفارغ الموجود في الموقع الرئيسي للمصنع.
عند إنشاء مرافق إنتاج جديدة ، تم إيلاء الكثير من الاهتمام لرفع مستوى وتنظيم الإنتاج. تم تنظيم إنتاج محرك الديزل وفقًا لمبدأ الخط والمجموعة ، مع مراعاة آخر إنجازات تلك الفترة في هذا المجال. تم استخدام أكثر الوسائل تقدمًا للميكنة والأتمتة لمعالجة الأجزاء وتجميعها ، والتي ضمنت إنشاء إنتاج ميكانيكي شامل لمحرك الديزل 5TDF.
في عملية تشكيل الإنتاج ، تم تنفيذ عمل مشترك كبير من التقنيين والمصممين لتحسين قابلية تصنيع تصميم محرك الديزل ، حيث أصدر الفنيون خلاله حوالي ستة آلاف اقتراح إلى KHKBD ، انعكس جزء كبير منها في توثيق تصميم المحرك.
من حيث المستوى الفني ، تجاوز إنتاج الديزل الجديد بشكل كبير مؤشرات مؤسسات الصناعة التي أنتجت منتجات مماثلة تم تحقيقها بحلول ذلك الوقت. وصل عامل المعدات لعمليات إنتاج الديزل 5TDF إلى قيمة عالية - 6 ، 22. في 3 سنوات فقط ، تم تطوير أكثر من 10 آلاف عملية تكنولوجية ، وتم تصميم وتصنيع أكثر من 50 ألف عنصر من المعدات. شارك عدد من الشركات التابعة لمجلس خاركوف الاقتصادي في تصنيع المعدات والأدوات ، من أجل مساعدة مصنع ماليشيف.
في السنوات اللاحقة (بعد عام 1965) ، في سياق الإنتاج التسلسلي لمحرك الديزل 5TDF ، نفذت الخدمات التكنولوجية للمصنع و TsNITI العمل لزيادة تحسين التقنيات من أجل تقليل كثافة اليد العاملة ، وتحسين جودة وموثوقية المحرك. محرك. موظفو TsNITI (المخرج Ya. A Shifrin ، كبير المهندسين B. N. Surnin) خلال 1967-1970. تم تطوير أكثر من 4500 اقتراح تقني ، مما يوفر انخفاضًا في كثافة اليد العاملة بأكثر من 530 ساعة قياسية وتقليلًا كبيرًا في الخسائر من الخردة أثناء الإنتاج. في الوقت نفسه ، جعلت هذه التدابير من الممكن خفض عدد عمليات التركيب والربط الانتقائي للأجزاء بأكثر من النصف. كانت نتيجة تنفيذ مجموعة من التصميمات والتدابير التكنولوجية تشغيلًا أكثر موثوقية وعالية الجودة للمحرك أثناء التشغيل مع وقت تشغيل مضمون يبلغ 300 ساعة. لكن عمل تقنيي المصنع و TsNITI ، جنبًا إلى جنب مع مصممي KHKBD ، استمر. كان من الضروري زيادة وقت تشغيل محرك 5TDF بمقدار 1.5 … 2.0 مرة. تم حل هذه المهمة أيضًا. تم تعديل محرك الديزل ذو الخزان ثنائي الأشواط 5TDF ودخل حيز الإنتاج في مصنع هندسة النقل في خاركوف.
لعب مدير المصنع O. A. Soich دورًا مهمًا للغاية في تنظيم إنتاج الديزل 5TDF ، بالإضافة إلى عدد من رواد الصناعة (D. F. Ustinov ، E. إنتاج الديزل ، وكذلك أولئك الذين شاركوا بشكل مباشر في حل المشكلات الفنية والتنظيمية.
جعلت أنظمة التسخين الذاتي وحقن الزيت من الممكن لأول مرة (في عام 1978) توفير بداية باردة لمحرك ديزل للدبابات عند درجات حرارة تقل عن -20 درجة مئوية (من 1984 إلى -25 درجة مئوية). في وقت لاحق (في عام 1985) أصبح من الممكن بمساعدة نظام PVV (سخان الهواء الداخل) تنفيذ بداية باردة لمحرك ديزل رباعي الأشواط (V-84-1) على خزانات T-72 ، ولكن فقط حتى درجة حرارة -20 درجة مئوية ، ولا يبدأ أكثر من عشرين ضمن مورد الضمان.
الأهم من ذلك ، انتقلت 5TDF بسلاسة إلى جودة جديدة في محركات الديزل من سلسلة 6TD (6TD-1 … 6TD-4) بمدى قدرة 1000-1500 حصان.وتجاوز نظائرها الأجنبية في عدد من المعايير الأساسية.
معلومات تشغيل المحرك
مواد التشغيل التطبيقية
النوع الرئيسي للوقود لتشغيل المحرك هو وقود محركات الديزل عالية السرعة GOST 4749-73:
عند درجة حرارة محيطة لا تقل عن + 5 درجة مئوية - ماركة DL ؛
في درجات الحرارة المحيطة من +5 إلى -30 درجة مئوية - علامات DZ ؛
عند درجة حرارة محيطة أقل من -30 درجة مئوية - ماركة DA.
إذا لزم الأمر ، يُسمح باستخدام وقود DZ في درجات حرارة محيطة أعلى من + 50 درجة مئوية.
بالإضافة إلى وقود محركات الديزل عالية السرعة ، يمكن للمحرك أن يعمل على وقود الطائرات TC-1 GOST 10227-62 أو بنزين المحرك A-72 GOST 2084-67 ، بالإضافة إلى خليط من الوقود المستخدم بأي نسب.
يستخدم الزيت M16-IHP-3 TU 001226-75 لتزييت المحرك. في حالة عدم وجود هذا الزيت ، يُسمح باستخدام زيت MT-16p.
عند التغيير من زيت إلى آخر ، يجب تصريف الزيت المتبقي من علبة المرافق للمحرك وخزان الزيت الخاص بالماكينة.
يحظر خلط الزيوت المستعملة مع بعضها وكذلك استخدام أنواع أخرى من الزيوت. يُسمح بخلط البقايا غير المستنزفة لعلامة تجارية واحدة من الزيت بأخرى ، معاد تعبئتها في نظام الزيت.
عند التصريف ، يجب ألا تقل درجة حرارة الزيت عن + 40 درجة مئوية.
لتبريد المحرك في درجة حرارة محيطة لا تقل عن + 5 درجات مئوية ، يتم استخدام مياه عذبة نقية بدون شوائب ميكانيكية ، ويتم تمريرها من خلال مرشح خاص يتم توفيره للمجموعة الأوروبية للجهاز.
لحماية المحرك من التآكل وتكوين النتوءات ، تتم إضافة 0.15٪ من مادة مضافة ثلاثية المكونات (0.05٪ من كل مكون) إلى الماء الذي يمر عبر الفلتر.
تتكون المادة المضافة من فوسفات ثلاثي الصوديوم GOST 201-58 ، ذروة الكروم البوتاسيوم GOST 2652-71 ونتريت الصوديوم GOST 6194-69 يجب أولاً إذابته في 5-6 لترات من الماء يمر عبر مرشح كيميائي ويتم تسخينه إلى درجة حرارة 60-80 درجة مئوية. في حالة التزود بالوقود من 2-3 لترات ، يُسمح (لمرة واحدة) باستخدام الماء بدون إضافات.
لا تصب المواد المضافة المضادة للتآكل مباشرة في النظام.
في حالة عدم وجود مادة مضافة ثلاثية المكونات ، يُسمح باستخدام ذروة الكروم النقي بنسبة 0.5 ٪.
عند درجة حرارة محيطة أقل من +50 درجة مئوية ، يجب استخدام سائل منخفض التجمد (مضاد للتجمد) "40" أو "65" GOST 159-52. العلامة التجارية المضادة للتجمد "40" تستخدم في درجات حرارة محيطة تصل إلى -35 درجة مئوية ، في درجات حرارة أقل من -35 درجة مئوية - مانع التجمد "65".
املأ المحرك بالوقود والزيت والمبرد وفقًا للإجراءات التي تمنع دخول الشوائب الميكانيكية والغبار والرطوبة إلى الوقود والزيت.
يوصى بإعادة التزود بالوقود بمساعدة الناقلات الخاصة أو جهاز التزود بالوقود العادي (عند التزود بالوقود من حاويات منفصلة).
يجب إعادة التزود بالوقود من خلال مرشح حريري. يوصى بملء الزيت بمساعدة حشوات زيت خاصة. قم بتعبئة الزيت والماء والسائل منخفض التجميد من خلال مرشح بشبكة رقم 0224 GOST 6613-53.
املأ الأنظمة بالمستويات المحددة في تعليمات تشغيل الجهاز.
لملء أحجام أنظمة التشحيم والتبريد بالكامل ، بعد التزود بالوقود ، قم بتشغيل المحرك لمدة 1-2 دقيقة ، ثم تحقق من المستويات ، وإذا لزم الأمر ، قم بإعادة تزويد الأنظمة بالوقود ،
أثناء التشغيل ، من الضروري التحكم في كمية سائل التبريد والزيت في أنظمة المحرك والحفاظ على مستويات IB ضمن الحدود المحددة.
لا تسمح للمحرك بالعمل إذا كان هناك أقل من 20 لترًا من الزيت في خزان تزييت المحرك.
إذا انخفض مستوى سائل التبريد بسبب التبخر أو تسرب إلى نظام التبريد ، أضف الماء أو مانع التجمد ، على التوالي.
قم بتصريف سائل التبريد والزيت من خلال صمامات الصرف الخاصة بالمحرك والماكينة (غلاية التسخين وخزان الزيت) باستخدام خرطوم مزود بفتحات حشو مفتوحة.لإزالة الماء المتبقي تمامًا من نظام التبريد لتجنب تجمده ، يوصى بسكب 5-6 لترات من سائل التجميد المنخفض على النظام.
ميزات تشغيل المحرك على أنواع مختلفة من الوقود
يتم تشغيل المحرك على أنواع مختلفة من الوقود من خلال آلية التحكم في تغذية الوقود التي لها موقعان لضبط ذراع الوقود المتعدد: التشغيل على الوقود لمحركات الديزل عالية السرعة ، ووقود المحركات النفاثة ، والبنزين (مع انخفاض القوة) ومخاليطهم بأي نسب ؛ تعمل فقط على البنزين.
يحظر تمامًا التشغيل على أنواع أخرى من الوقود مع وضع الرافعة هذا.
يتم تركيب آلية التحكم في تغذية الوقود من الوضع "التشغيل على وقود الديزل" إلى الوضع "التشغيل على البنزين" عن طريق تدوير المسمار اللولبي للرافعة متعددة الوقود في اتجاه عقارب الساعة حتى تتوقف ، ومن الوضع "التشغيل على البنزين "إلى الوضع" التشغيل على وقود الديزل "- عن طريق تدوير المسمار اللولبي لضبط ذراع الوقود المتعدد عكس اتجاه عقارب الساعة حتى يتوقف.
ميزات بدء وتشغيل المحرك عند العمل بالبنزين. قبل بدء تشغيل المحرك بدقيقتين على الأقل ، من الضروري تشغيل مضخة BCN في الماكينة وضخ الوقود بشكل مكثف باستخدام مضخة التحضير اليدوية للآلة ؛ في جميع الأحوال ، بغض النظر عن درجة الحرارة المحيطة ، قبل البدء ، قم بحقن الزيت مرتين في الأسطوانات.
يجب أن تظل مضخة الطرد المركزي للبنزين في الماكينة قيد التشغيل طوال الوقت الذي يعمل فيه المحرك بالبنزين ، وخلائطه مع أنواع الوقود الأخرى ، وأثناء التوقفات القصيرة (3-5 دقائق) للآلة.
الحد الأدنى لسرعة التباطؤ الثابت عند تشغيل المحرك بالبنزين هي 1000 في الدقيقة.
ميزات العملية
يتذكر S. Suvorov مزايا وعيوب هذا المحرك في كتابه "T-64".
على دبابات T-64A ، التي تم إنتاجها منذ عام 1975 ، تم أيضًا تعزيز درع البرج بسبب استخدام حشو اكسيد الالمونيوم.
في هذه الآلات ، تمت زيادة سعة خزانات الوقود أيضًا من 1093 لترًا إلى 1270 لترًا ، مما أدى إلى ظهور صندوق لتخزين قطع الغيار في الجزء الخلفي من البرج. في آلات الإصدارات السابقة ، تم وضع قطع الغيار والملحقات في صناديق على الرفارف اليمنى ، حيث تم تركيب خزانات وقود إضافية ، متصلة بنظام الوقود. عندما قام السائق بتثبيت صمام توزيع الوقود على أي مجموعة من الخزانات (الخلفية أو الأمامية) ، تم إنتاج الوقود بشكل أساسي من الخزانات الخارجية.
تم استخدام زوج من التروس الدودية في آلية شد الجنزير ، مما سمح بتشغيله دون صيانة طوال فترة خدمة الخزان بأكملها.
تم تحسين خصائص أداء هذه الآلات بشكل كبير. لذلك ، على سبيل المثال ، تمت زيادة التجربة قبل خدمة الرقم التالي من 1500 و 3000 كم إلى 2500 و 5000 كم لـ T01 و TO ، على التوالي. للمقارنة ، تم تنفيذ الخزان T-62 TO1 TO2 بعد 1000 و 2000 كم من التشغيل ، وعلى دبابة T-72 - بعد 1600-1800 و 3300-3500 كم من التشغيل ، على التوالي. تمت زيادة فترة الضمان لمحرك 5TDF من 250 إلى 500 ساعة ، وكانت فترة الضمان للجهاز بأكمله 5000 كم.
لكن المدرسة ليست سوى مقدمة ، فقد بدأت العملية الرئيسية في القوات ، حيث انتهى بي الأمر بعد تخرجي من الكلية عام 1978. قبل التخرج بقليل ، تم إبلاغنا بأمر القائد العام للقوات البرية بأنه يجب توزيع خريجي مدرستنا فقط على التشكيلات التي توجد بها دبابات T-64. كان هذا بسبب حقيقة أن القوات كانت هناك حالات فشل جماعي لدبابات T-64 ، على وجه الخصوص ، محركات 5TDF. السبب - الجهل بالمواد وقواعد تشغيل هذه الخزانات. كان اعتماد دبابة T-64 مشابهًا للتحول في الطيران من المحركات المكبسية إلى المحركات النفاثة - يتذكر قدامى المحاربين في مجال الطيران كيف كان ذلك.
بالنسبة لمحرك 5TDF ، كان هناك سببان رئيسيان لفشل القوات - ارتفاع درجة الحرارة وتآكل الغبار. كان كلا السببين بسبب الجهل أو الإهمال لقواعد التشغيل.العيب الرئيسي لهذا المحرك هو أنه ليس مصممًا جدًا للحمقى ، وأحيانًا يتطلب منهم القيام بما هو مكتوب في تعليمات التشغيل. عندما كنت بالفعل قائدًا لسرية دبابات ، بدأ أحد قادة فصيلتي ، خريج مدرسة تشيليابينسك للدبابات ، التي دربت الضباط على دبابات T-72 ، بطريقة ما في انتقاد محطة توليد الكهرباء في دبابة T-64. لم يعجبه المحرك وتكرار صيانته. ولكن عندما سُئل السؤال "كم مرة في ستة أشهر قمت بفتح أسقف MTO على خزانات التدريب الثلاثة الخاصة بك ونظرت في حجرة ناقل الحركة بالمحرك؟" اتضح أنه لم يحدث. وذهبت الدبابات وقدمت تدريبات قتالية.
وهكذا بالترتيب. حدث ارتفاع درجة حرارة المحرك لعدة أسباب. أولاً ، نسي الميكانيكي إزالة الحصيرة من المبرد ثم لم ينظر إلى الأدوات ، لكن هذا حدث نادرًا جدًا ، وكقاعدة عامة ، في الشتاء. والثاني والرئيسي هو الحشو بسائل التبريد. وفقًا للتعليمات ، من المفترض أن تملأ المياه (خلال فترة التشغيل الصيفية) بمادة مضافة ثلاثية المكونات ، ويجب ملء الماء من خلال مرشح كبريتيد خاص ، تم تجهيز جميع آلات الإطلاق المبكر به ، وعلى جديد. تم إصدار فلتر واحد لكل شركة (10-13 خزان). فشلت المحركات ، بشكل رئيسي من خزانات مجموعة التدريب ، والتي تم تشغيلها خمسة أيام على الأقل في الأسبوع وعادة ما تكون موجودة في نطاقات في الحدائق الميدانية. في الوقت نفسه ، فإن "الكتب المدرسية" لميكانيكا السائقين (ما يسمى بآليات التدريب) ، كقاعدة عامة ، العمال الجادون والرجال ذوو الضمير ، ولكنهم لا يعرفون تعقيدات المحرك ، يمكنهم أحيانًا تحمل تكلفة صب الماء في نظام التبريد فقط من الحنفية ، خاصة وأن الفلتر الكبريت (وهو واحد لكل شركة) كان يتم الاحتفاظ به عادةً في الفصول الشتوية ، في مكان ما في خزانة المدير الفني للشركة. والنتيجة هي تكوين مقياس في القنوات الرقيقة لنظام التبريد (في منطقة غرف الاحتراق) ، ونقص دوران السائل في الجزء الأكثر سخونة من المحرك ، وارتفاع درجة الحرارة ، وفشل المحرك. تفاقم تكوين القشور بسبب حقيقة أن الماء في ألمانيا صعب للغاية.
بمجرد الوصول إلى وحدة مجاورة ، تمت إزالة المحرك بسبب ارتفاع درجة الحرارة بسبب خطأ السائق. بعد أن وجد تسربًا صغيرًا لسائل التبريد من المبرد ، بناءً على نصيحة أحد "الخبراء" لإضافة الخردل إلى النظام ، اشترى علبة من الخردل في المتجر وسكبها بالكامل في النظام ، نتيجة لذلك - انسداد القنوات وفشل المحرك.
كانت هناك أيضًا مفاجآت أخرى مع نظام التبريد. فجأة ، يبدأ في طرد المبرد من نظام التبريد من خلال صمام بخار الهواء (PVK). البعض ، الذين لا يفهمون ما هو الأمر ، يحاولون بدء تشغيله من القاطرة - نتيجة تدمير المحرك. وهكذا ، جعلني نائب رئيس كتيبي "هدية" للعام الجديد ، واضطررت إلى تغيير المحرك في الحادي والثلاثين من كانون الأول (ديسمبر). كان لدي وقت قبل العام الجديد ، لأنه إن استبدال المحرك على خزان T-64 ليس إجراءً معقدًا للغاية ، والأهم من ذلك أنه لا يتطلب محاذاة عند تثبيته. معظم الوقت عند استبدال محرك على خزان T-64 ، كما هو الحال في جميع الخزانات المحلية ، يتم إجراؤه من خلال إجراء تفريغ وإعادة تعبئة الزيت والمبرد. إذا كانت خزاناتنا تحتوي على موصلات بصمامات بدلاً من توصيلات durit ، كما هو الحال في Leopards أو Leclercs ، فإن استبدال المحرك على خزانات T-64 أو T-80 في الوقت المناسب لن يستغرق أكثر من استبدال وحدة الطاقة بالكامل في الخزانات الغربية. على سبيل المثال ، في ذلك اليوم الذي لا يُنسى ، 31 ديسمبر 1980 ، بعد تجفيف الزيت والمبرد ، "رميت" أنا والضابط الصف إي. سوكولوف المحرك من MTO في 15 دقيقة فقط.
السبب الثاني لفشل محركات 5TDF هو تآكل الغبار. نظام تنقية الهواء. إذا لم تتحقق من مستوى سائل التبريد في الوقت المناسب ، ولكن يجب فحصه قبل كل خروج من الماكينة ، فقد تأتي لحظة لا يوجد فيها سائل في الجزء العلوي من سترة التبريد ، ويحدث ارتفاع درجة حرارة محلية. في هذه الحالة ، أضعف نقطة هي الفوهة.في هذه الحالة ، تحترق جوانات الحاقن أو يفشل الحاقن نفسه ، ثم من خلال الشقوق الموجودة فيه أو الحشيات المحترقة ، تخترق الغازات من الأسطوانات إلى نظام التبريد ، وتحت ضغطها يتم طرد السائل عبر PVCL. كل هذا ليس قاتلاً للمحرك ويتم التخلص منه إذا كان هناك شخص مطلع في الوحدة. في المحركات التقليدية على الخط وعلى شكل V في وضع مماثل ، "يقود" حشية رأس الأسطوانة ، وفي هذه الحالة سيكون هناك المزيد من العمل.
إذا توقف المحرك في مثل هذه الحالة ولم يتم اتخاذ أي تدابير ، فبعد فترة من الوقت ستبدأ الأسطوانات بالملء بسائل التبريد ، يكون المحرك عبارة عن شبكة بالقصور الذاتي ومنظف هواء إعصاري. منظف الهواء ، وفقًا لتعليمات التشغيل ، يتم شطفه حسب الحاجة. على خزانات من نوع T-62 ، يتم غسلها في الشتاء بعد 1000 كم ، وفي الصيف بعد 500 كم. على دبابة T-64 - حسب الحاجة. هذا هو المكان الذي يأتي فيه حجر العثرة - اعتبره البعض حقيقة أنه ليس عليك غسله على الإطلاق. نشأت الحاجة عندما دخل النفط في الأعاصير. وإذا احتوت واحدة على الأقل من 144 إعصارًا على زيت ، فيجب شطف منظف الهواء ، لأن من خلال هذا الإعصار ، يدخل الهواء غير النظيف مع الغبار إلى المحرك ، وبعد ذلك ، مثل الصنفرة ، يتم محو بطانات الأسطوانات وحلقات الكباس. يبدأ المحرك في فقدان الطاقة ، ويزداد استهلاك الزيت ، ثم يتوقف عن بدء التشغيل تمامًا.
ليس من الصعب التحقق من دخول الزيت إلى الأعاصير - فقط انظر إلى مداخل الإعصار في منظف الهواء. عادة ما ينظرون إلى أنبوب تصريف الغبار من منظف الهواء ، وإذا وجد الزيت فيه ، فإنهم ينظرون إلى منظف الهواء ، وإذا لزم الأمر ، يغسلونه. من أين أتى الزيت؟ الأمر بسيط: يوجد عنق حشو خزان الزيت في نظام تزييت المحرك بجوار شبكة سحب الهواء. عند التزود بالوقود بالزيت ، عادة ما يتم استخدام إبريق الري ، ولكن منذ ذلك الحين مرة أخرى ، على آلات التدريب ، كانت علب الري ، كقاعدة عامة ، غائبة (فقد شخص ما ، أو قام شخص ما بوضعه على حزام كاتربيلر ، ونسيها ومر بها ، وما إلى ذلك) ، ثم قام الميكانيكيون ببساطة بسكب الزيت من الدلاء ، بينما انسكب الزيت ، سقطت أولاً على شبكة سحب الهواء ، ثم في منظف الهواء. حتى عند ملء الزيت من خلال علبة سقي ، ولكن في الطقس العاصف ، قامت الرياح برش الزيت على شبكة منظف الهواء. لذلك ، عند إعادة التزود بالوقود بالوقود ، طلبت من مرؤوسي وضع بساط من قطع الغيار وملحقات الخزان على شبكة سحب الهواء ، ونتيجة لذلك تجنبت مشكلة تآكل الغبار للمحرك. وتجدر الإشارة إلى أن الظروف المتربة في ألمانيا في الصيف كانت الأشد. لذلك ، على سبيل المثال ، أثناء تدريبات الفرقة في أغسطس 1982 ، عند القيام بمسيرة عبر مناطق إزالة الغابات في ألمانيا ، بسبب الغبار المعلق ، لم يكن مرئيًا حتى أين انتهى ماسورة مسدس دبابته. تم الحفاظ على المسافة بين السيارات في العمود حرفيًا عن طريق الرائحة. عندما تبقى بضعة أمتار من الخزان الرئيسي ، كان من الممكن تمييز رائحة غازات العادم والفرامل في الوقت المناسب. وهكذا 150 كيلومترًا. بعد المسيرة ، كان كل شيء: الدبابات والأشخاص ووجوههم ، وزرةهم وأحذيتهم من نفس اللون - لون غبار الطريق.
ديزل 6 تي دي
بالتزامن مع التصميم والتحسين التكنولوجي لمحرك الديزل 5TDF ، بدأ فريق التصميم KKBD في تطوير النموذج التالي لمحرك ديزل ثنائي الأشواط في تصميم بست أسطوانات بقوة أكبر تصل إلى 735 كيلو واط (1000 حصان). كان هذا المحرك ، مثل محرك 5TDF ، محرك ديزل مع أسطوانات مرتبة أفقيًا ومكابس ذات حركة عكسية ونفخ مباشر. تم تسمية الديزل 6TD.
تم تنفيذ الشحن التوربيني من ضاغط ميكانيكي (زنبركي) متصل بالتوربينات الغازية ، مما أدى إلى تحويل جزء من الطاقة الحرارية لغازات العادم إلى عمل ميكانيكي لتشغيل الضاغط.
نظرًا لأن الطاقة التي طورها التوربين لم تكن كافية لتشغيل الضاغط ، فقد تم توصيله بكل من أعمدة الكرنك للمحرك باستخدام علبة تروس وآلية نقل.تم أخذ نسبة الضغط لتكون 15.
للحصول على توقيت الصمام المطلوب ، والذي يتم فيه توفير التنظيف الضروري للأسطوانة من غازات العادم والتعبئة بالهواء المضغوط ، تم توفير إزاحة زاوية لأعمدة الكرنك (كما في محركات 5TDF) جنبًا إلى جنب مع الترتيب غير المتماثل للمدخل ومنافذ عادم الاسطوانات بطولها. يبلغ عزم الدوران المأخوذ من أعمدة الكرنك 30٪ لعمود السحب و 70٪ لعادم عزم دوران المحرك. تم نقل عزم الدوران الذي تم تطويره على عمود السحب من خلال ناقل الحركة إلى عمود العادم. يمكن أخذ عزم الدوران الكلي من كلا طرفي عمود العادم من خلال قابض قوة الإقلاع.
في أكتوبر 1979 ، نجح محرك 6TD ، بعد مراجعة جادة لمجموعة الأسطوانات المكبس ، ومعدات الوقود ، ونظام إمداد الهواء وعناصر أخرى ، في اجتياز الاختبارات بين الأقسام بنجاح. منذ عام 1986 ، تم تصنيع أول 55 سلسلة محركات. في السنوات اللاحقة ، زاد الإنتاج التسلسلي وبلغ ذروته في عام 1989.
كانت النسبة المئوية للتوحيد الجزئي للنسخة 6TD مع محرك الديزل 5TDF أكثر من 76 ٪ ، ولم تكن موثوقية التشغيل أقل من تلك الخاصة بـ 5TDF ، والتي تم إنتاجها بكميات كبيرة لسنوات عديدة.
استمر عمل KHKBD تحت قيادة كبير المصممين N. K. Ryazantsev لزيادة تحسين محرك الديزل ثنائي الأشواط. تم الانتهاء من الوحدات والآليات والأنظمة ، والتي تم بموجبها تحديد العيوب الفردية أثناء التشغيل. تم تحسين نظام الضغط. تم إجراء العديد من اختبارات مقاعد البدلاء للمحركات مع إدخال تغييرات على التصميم.
تم تطوير تعديل جديد لمحرك الديزل ، 6TD-2. لم تعد قوتها 735 كيلو واط (1000 حصان) ، كما في 6 تي دي ، ولكن 882 كيلو واط (1200 حصان). تم توفير توحيدها التفصيلي مع محرك الديزل 6TD بأكثر من 90٪ ، ومحرك الديزل 5TDF - أكثر من 69٪.
على عكس محرك 6TD ، استخدم محرك 6TD-2 ضاغط طرد مركزي من مرحلتين لنظام الضغط والتغييرات في تصميم التوربين والمنافخ وفلتر زيت الطرد المركزي والأنبوب الفرعي والوحدات الأخرى. تم أيضًا تقليل نسبة الضغط بشكل طفيف - من 15 إلى 14.5 وزاد متوسط الضغط الفعال من 0.98 ميجا باسكال إلى 1.27 ميجا باسكال. كان استهلاك الوقود المحدد لمحرك 6TD-2 220 جم / (كيلوواط * ساعة) (162 جم / (حصان * ساعة)) بدلاً من 215 جم / (كيلو واط * ساعة) (158 جم / (حصان * ساعة)) - لـ 6 تي دي. من وجهة نظر التركيب في الخزان ، كان محرك الديزل 6TD-2 قابلاً للتبديل تمامًا مع محرك 6DT.
في عام 1985 ، اجتاز ديزل 6TD-2 الاختبارات المشتركة بين الأقسام وتم تقديم وثائق التصميم لإعداد وتنظيم الإنتاج التسلسلي.
في KKBD ، بمشاركة NIID ومنظمات أخرى ، استمرت أعمال البحث والتطوير على محرك الديزل ثنائي الأشواط 6TD بهدف زيادة قوتها إلى 1103 كيلو واط (1500 حصان) ، 1176 كيلو واط (1600 حصان) ، 1323 كيلو واط (1800 حصان) مع الاختبار على العينات ، وكذلك إنشاء مجموعة من محركات VGM وآلات الاقتصاد الوطني على أساسها. بالنسبة لفئة VGM من فئة الوزن الخفيف والمتوسط ، تم تطوير محركات ديزل 3TD بسعة 184 … 235 كيلوواط (250-320 حصانًا) ، 4 تي دي بسعة 294 … 331 كيلو واط (400 … 450 حصانًا). كما تم تطوير متغير لمحرك ديزل 5DN بسعة 331 … 367 كيلو واط (450-500 حصان) للمركبات ذات العجلات. بالنسبة لناقلات الجرارات والمركبات الهندسية ، تم تطوير مشروع لمحرك ديزل 6DN بسعة 441 … 515 كيلو واط (600-700 حصان).
ديزل 3 تي دي
محركات ZTD ذات التصميم ثلاثي الأسطوانات هي أعضاء في سلسلة موحدة مع محركات تسلسلية 5TDF و 6TD-1 و 6TD-2E. في أوائل الستينيات ، تم إنشاء عائلة محركات تعتمد على 5TDF في خاركوف للمركبات الخفيفة الوزن (ناقلات الجنود المدرعة ، ومركبات القتال المشاة ، وما إلى ذلك) وفئة الوزن الثقيل (الدبابات ، 5TDF ، 6TD).
هذه المحركات لها مخطط تصميم واحد:
- دورة ثنائية الشوط
- ترتيب الاسطوانات الأفقي.
- الاكتناز العالي
- انتقال الحرارة المنخفضة
- القدرة على الاستخدام في درجات الحرارة المحيطة
البيئات من -50 إلى + 55 درجة مئوية ؛
- خفض الطاقة المنخفضة عند درجات الحرارة العالية
البيئة؛
- متعدد الوقود.
بالإضافة إلى الأسباب الموضوعية ، تم ارتكاب أخطاء في إنشاء عائلة من محركات الديزل ثنائية الأشواط 3TD في منتصف الستينيات. تم اختبار فكرة المحرك ذو 3 أسطوانات على أساس 5 أسطوانات حيث تم إخماد أسطوانتين. في الوقت نفسه ، لم يتم تنسيق مسار الغاز الجوي ووحدات الضغط. وبطبيعة الحال ، زادت قوة الخسائر الميكانيكية أيضًا.
كانت العقبة الرئيسية أمام إنشاء عائلة موحدة من المحركات في الستينيات والسبعينيات من القرن الماضي هي عدم وجود برنامج واضح لتطوير بناء المحركات في الدولة ؛ كانت القيادة "تقذف" بين المفاهيم المختلفة لمحركات الديزل ومحركات التوربينات الغازية. في السبعينيات ، عندما تولى ليونيد بريجنيف قيادة البلاد ، أصبح الوضع أكثر تفاقمًا ، والإنتاج الموازي للدبابات بمحركات مختلفة - T-72 و T-80 ، والتي كانت وفقًا لخصائصها "دبابات مماثلة" أنتجت بالفعل T- 64. لم يعد هناك حديث عن توحيد محركات الدبابات وعربات المشاة القتالية وناقلات الجند المدرعة.
لسوء الحظ ، كان الوضع نفسه في الفروع الأخرى للمجمع الصناعي العسكري - في نفس الوقت ، تم تطوير العديد من مكاتب التصميم في صناعة الصواريخ ، وبناء الطائرات ، بينما لم يتم اختيار الأفضل من بينها ، ولكن المنتجات المماثلة من مكاتب تصميم مختلفة (مكتب التصميم) تم إنتاجه بالتوازي.
كانت مثل هذه السياسة بداية نهاية الاقتصاد المحلي ، وسبب التأخر في بناء الدبابات ، بدلاً من الاتحاد في "قبضة واحدة" ، تبعثرت الجهود على التطوير الموازي لمكاتب التصميم المتنافسة.
المركبات الخفيفة (LME) ، التي تم إنتاجها في الستينيات … الثمانينيات من القرن الماضي ، لديها محركات ذات تصميم قديم ، مما يوفر كثافة طاقة في حدود 16-20 حصان / طن. يجب أن تتمتع الآلات الحديثة بقوة معينة تتراوح بين 25 و 28 حصانًا / طنًا ، مما يزيد من قدرتها على المناورة.
في التسعينيات ، 2000 ، أصبح تحديث LME مناسبًا - BTR-70 ، BTR-50 ، BMP-2.
خلال هذه الفترة ، تم إجراء اختبارات لهذه الآلات ، والتي أظهرت الخصائص العالية للمحرك الجديد ، ولكن في الوقت نفسه ، تم تخزين عدد كبير من محركات UTD-20S1 وإنتاجها على أراضي أوكرانيا بعد الانهيار. من اتحاد الجمهوريات الاشتراكية السوفياتية.
المصمم العام لمبنى الخزان الأوكراني M. D. قرر Borisyuk (KMDB) استخدام المحركات التسلسلية الحالية - SMD-21 UTD-20 والألمانية "Deutz" لتحديث هذه الآلات.
كان لكل مركبة محركاتها الخاصة التي لم يتم توحيدها مع بعضها البعض ومع المحركات الموجودة بالفعل في الجيش. والسبب هو أنه من المربح لمصانع الإصلاح التابعة لوزارة الدفاع استخدام المحركات المتوفرة في مستودعات العميل ، مما يقلل من تكلفة العمل.
لكن هذا المنصب حرم من عمل "مصنع المؤسسة العامة" الذي يحمل اسم V. A. Malysheva "وقبل كل شيء النبات الكلي.
اتضح أن هذا الموقف غامض - من ناحية ، المدخرات ، من ناحية أخرى ، فقدان المنظور.
تجدر الإشارة إلى أنه في KMDB فيما يتعلق بـ 3TD ، تم تقديم عدد من المطالبات (للضوضاء والدخان) ، والتي تم قبولها وإزالتها.
من أجل تقليل الدخان أثناء بدء التشغيل وفي أوضاع عابرة ، تم تثبيت معدات الوقود المغلقة على محرك ZTD وتم تقليل استهلاك الزيت بشكل كبير. يتم ضمان تقليل الضوضاء من خلال تقليل أقصى ضغط الاحتراق وتقليل الخلوص في زوج أسطوانة المكبس في محركات بقوة 280 و 400 حصان ، بالإضافة إلى تقليل نطاق الاهتزازات الالتوائية
تم تقليل استهلاك الزيت على محركات ZTD بسبب العوامل التالية:
- تقليل عدد الاسطوانات ؛
- استخدام مكبس بهيكل من الحديد الزهر بدلاً من سبيكة الألومنيوم ؛
- زيادة الضغط النوعي لحلقة مكشطة الزيت بمقدار
جدار الاسطوانة.
كنتيجة للتدابير المتخذة ، فإن الاستهلاك النسبي للزيت على المحركات ZTD يقترب من الاستهلاك على المحركات للأغراض الاقتصادية الوطنية.