تم دمج حب الوطن من النخبة الصناعية السوفيتية مع المسؤولية المشتركة عن النتيجة النهائية
لم يكن التفاعل بين الصناعة في جميع الأوقات - سواء في الإمبراطورية الروسية أو في الاتحاد السوفياتي أو اليوم - ينتمي إلى نقاط القوة في الصناعة المحلية. على عكس ألمانيا أو الولايات المتحدة ، حيث كان للالتزامات التعاقدية قوة ثابتة وشبه مقدسة.
خذ على سبيل المثال العلاقة بين علماء المعادن الروس وبناة الآلات. في النصف الثاني من القرن التاسع عشر ، لم تتلق مصانع هندسة النقل الجديدة وأحواض بناء السفن الكمية المطلوبة من المعادن الصناعية من عمال المناجم في الأورال. اعتبر الأخير أنه من غير المربح إنتاج الكثير من المنتجات المدلفنة الرخيصة نسبيًا ، حيث تم توفير نفس الربح من خلال حجم أصغر بكثير من حديد التسقيف الباهظ الثمن. كان لابد من شراء المعدن المفقود لمحاور السيارة وأعمدة المحرك وجلد السفينة من الخارج. بحلول نهاية القرن فقط ، تم حل المشكلة عن طريق مصانع التعدين الروسية الجنوبية ، التي أسسها الصناعيون البلجيكيون أو الفرنسيون. في جبال الأورال ، بنى الفرنسيون أيضًا مصنعًا واحدًا - Chusovskaya.
يبدو أنه في الحقبة السوفيتية ، كانت هذه النزوات غير واردة. بالإضافة إلى ذلك ، زودت مصانع التعدين التي بنيت في الثلاثينيات البلاد بالمعادن ككل. ومع ذلك ، في كل مرة طلب فيها صانعو الآلات أنواعًا معقدة جديدة من المنتجات المدلفنة ، كان علماء المعادن يتقنونها لسنوات ، أو حتى عقود.
الإقطاع الإداري
دعنا ننتقل إلى تاريخ Uralvagonzavod. بالفعل في مشاريعها الأولى ، تم التخطيط لاستخدام عجلات فولاذية مدلفنة صلبة تحت السيارات ذات المحاور الأربعة حيث وصلت القدرة التصميمية إلى قدرتها التصميمية ، والتي تم التخطيط لموردها إلى مصنع Novo-Tagil Metallurgical القريب. ومع ذلك ، تم بناء هذا الأخير من قبل قسم المعادن ، وأرجأ بناء مطحنة الدرفلة إلى 1938-1942 ، وليس في المقام الأول. ونتيجة لذلك ، لم تبدأ القضية قبل الحرب. وبعد الحرب ، لم يكن استئجار العجلات مهتمًا جدًا بعلماء المعادن. النتيجة: حتى منتصف الخمسينيات من القرن الماضي ، غادرت سيارات تاجيل المصنع على عجلات قصيرة العمر من الحديد الزهر بدلاً من العجلات الفولاذية. تسبب هذا في خسائر فادحة لعمال السكك الحديدية ، لكن لم يكن هناك خيار: إما مثل هذه السيارات أو لا شيء.
حدث الشيء نفسه مع إدخال الفولاذ منخفض السبائك في مبنى النقل. لقد وعدوا بتخفيض ملحوظ في الوزن الساكن للمعدات الدارجة مع الحفاظ على جميع خصائص الأداء. بدأ مصممو Uralvagonzavod في تصميم سيارات مصنوعة من معدن منخفض السبائك في نهاية الثلاثينيات ، لكن إنتاجهم التسلسلي لم يبدأ إلا في النصف الثاني من الخمسينيات ، نظرًا لأن علماء المعادن لم يقدموا المنتجات المدلفنة المناسبة أو السبائك الحديدية لأجزاء الصب.
يجب أن يقال أن فيروس الإقطاع الإداري أثر على صانعي الآلات أنفسهم. في صيف عام 1937 ، حدثت قصة مثيرة ميزت العلاقات بين الوكالات في ذلك الوقت. أرسلت المديرية الرئيسية للمشاريع المعدنية إلى Uralvagonzavod طلبًا بخمسة آلاف طن من الفراغات لمصنع الضمادات الذي تم إطلاقه مؤخرًا في مصنع Novo-Tagil. كانت المديرية الرئيسية لهندسة النقل غاضبة من التعدي على مؤسسة تابعة. نائب رئيس المديرية الرئيسية ج.في 11 يوليو أرسل ألكساندروف رسالة إلى GUMP و Uralvagonzavod بالبيان التالي: "نحن مندهشون للغاية من أن حل قضية مهمة مثل تنظيم إنتاج ضمادة فارغة في Uralvagonzavod تم تنفيذه بدون مشاركتنا ، بل وأكثر من ذلك. - لم نرسل حتى نسخة من الزي إلى Uralvagonzavod … أطلب منكم إنشاء إجراء صارم لإصدار الفراغات لمصانعنا فقط بالاتفاق معنا ومن خلال Glavtransmash ".
ونتيجة لذلك ، حُرم علماء المعادن من ضمادة الفولاذ ، ويُزعم أنه بسبب الاستحالة الفنية لصب سبائك عالية الجودة في متجر الموقد المفتوح في Uralvagonzavod. في هذه الأثناء ، بالفعل في عام 1936 ، تم صب الفراغ المحوري هنا ، وفي عام 1937 - سبائك لدرفلة الألواح. لذلك ، كان لا بد من نقل سبائك مطحنة الكفن ، التي تقع على بعد بضعة كيلومترات من UVZ ، من نباتات Vyksa و Kuznetsk. علاوة على ذلك ، فقد تركت جودتها الكثير مما هو مرغوب فيه ، وكانت أحجام الإمدادات غير كافية.
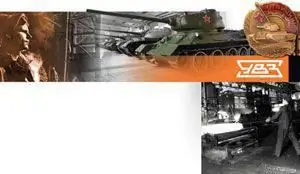
في عام 1938 ، أعاد التاريخ نفسه. كان المستهلك الرئيسي لسبائك UVZ هو مصنع مولوتوف (أي بيرم) للمدفعية ، والذي حصل على مجموعة من الفراغات في نهاية العام. ولم يذهب سوى عدد قليل منهم إلى متجر الضمادات ، والذي اضطر مرة أخرى إلى استيراد المعدن المفقود لمدة ألفين أو ألفين ونصف كيلومتر. سادت مصالح الصناعة في توزيع الصلب Uralvagonzavodsk بشكل واضح.
لم يسلم مرض الأقسام صناعة الدفاع أيضًا. العديد من المنشورات حول تاريخ بناء الدبابات السوفيتية مليئة بأمثلة عن كيفية تأخر بناء النماذج الأولية أو نشر الإنتاج الضخم بسبب عدم تسليم المعدن ، وخاصة الدروع.
وحتى اليوم ، لم تذهب المصلحة الذاتية القطاعية إلى أي مكان ، لقد غيرت شكلها فقط. طلبات الحصول على أشكال جديدة من المنتجات المدرفلة يتم محاربتها ببساطة بأسعار باهظة. ليست هناك حاجة للحديث عن سياسة منسقة. بعد انهيار سعر صرف الروبل في مطلع 2014-2015 ، رفعت شركات المعادن أسعار عربات السكك الحديدية بنسبة 30-60٪. وبدأوا على الفور في الشكوى من صانعي الآلات للمعدات التي ارتفعت أسعارها - بعد كل شيء ، يتم إنتاج الآلات في روسيا وليست مرتبطة بسعر صرف الدولار.
يبدو أنه يوجد في بلدنا علاج واحد فقط للمشاكل المشتركة بين القطاعات: إنشاء أنظمة متكاملة رأسياً ، حيث يتم تحويل الخام المستخرج من قبل قواتنا أولاً إلى معدن ثم إلى آلات مكتملة.
وحدة زمن الحرب
ومع ذلك ، هناك فترة قصيرة في تاريخنا تراجعت فيها مصالح الصناعة إلى الخلفية. نحن نتحدث عن الحرب الوطنية العظمى. تم الجمع بين الوطنية غير المشكوك فيها للنخبة الصناعية السوفيتية في ذلك الوقت مع المسؤولية المشتركة لجميع المشاركين في الإنتاج الدفاعي عن النتيجة النهائية. أي أن مدير مصنع الدرفلة المدرعة لم يكن مسؤولاً عن حجم الفولاذ المصهور والملفوف بقدر ما كان مسؤولاً عن عدد الخزانات التي تم بناؤها.
تم اتخاذ الخطوة الرئيسية في هذا الاتجاه من قبل مدير NII-48 A. S. Zavyalov. في الأيام الأولى للحرب ، التفت إلى الحكومة باقتراح لإصدار تعليمات للمعهد لإدخال تقنيات لإنتاج الفولاذ الخاص والهياكل المدرعة في الشركات في شرق البلاد ، والتي شاركت لأول مرة في تصنيع المدرعات. مركبات. في أوائل يوليو ، ترأس فريق من المتخصصين من NII-48 إعادة الهيكلة التكنولوجية لأكبر 14 شركة. من بينها مصانع Magnitogorsk و Kuznetsk Metallurgical و Novo-Tagil و Chusovka Metallurgical Plants و Ural Heavy Machine Building Plant و Gorky Krasnoye Sormovo و Stalingrad Tractor Plant و Stalingrad Red October و No. 264. وهكذا ، انتهك Zavyalov محرمات ما قبل الحرب: تضمنت القائمة شركات تابعة للمفوضيات الثلاث.
زودت الوطنية والقمع الإجباري للأنانية الإدارية علم المعادن السوفيتي بمعدلات غير مسبوقة من تطوير المنتجات الدفاعية ، لا في فترة ما قبل الحرب ولا في فترة ما بعد الحرب.في غضون أشهر ، في شرق البلاد (بشكل أساسي في جبال الأورال) ، تم تنظيم إنتاج المنغنيز الحديدي ، والفيروسيليكون ، والفيروكروم ، والفيروفاناديوم والسبائك الأخرى ، والتي بدونها من المستحيل الحصول على الفولاذ المدرع. بعد خسارة المناطق الغربية ، ظلت تشيليابينسك المصنع الوحيد للسبائك الحديدية في الاتحاد السوفياتي. على ذلك ، في وقت قصير ، تمت زيادة الصهر مرتين ونصف. تم إنتاج 25 نوعًا من المنتجات ، ولكن معظمها كان من أنواع مختلفة من الفيروكروم. تم إنشاء صهر المنغنيز الحديدي في أفران الصهر ، وليس فقط في أفران الصهر القديمة ذات الحمولة المنخفضة لنباتي نيجني تاجيل وكوشفينسكي ، ولكن أيضًا في فرن كبير حديث من مجموعة Magnitogorsk. على عكس جميع أفكار ما قبل الحرب ، تم صهر الكروم في النصف الثاني من عام 1941 في أفران الصهر الخاصة بهم بواسطة علماء المعادن من نباتات نيجني تاجيل وسيروف ، وقدم علماء من فرع الأورال لأكاديمية العلوم في اتحاد الجمهوريات الاشتراكية السوفياتية مساعدة كبيرة في إنشاء تقنية. في وقت لاحق ، تم إتقان صهر الفيروسيليكون في أفران سيروف العالية.
لم تكن هناك معسكرات مدرعة سواء في جبال الأورال أو في غرب سيبيريا قبل الحرب ، وكان لا بد من نقلهم على عجل من المؤسسات التي كانت في منطقة القتال.
في صيف عام 1941 ، كانت المعدات التي تم إخلاؤها لا تزال قيد النقل. ثم اقترح كبير ميكانيكي Magnitogorsk Combine N. A. Ryzhenko دحرجة الدرع على طاحونة مزدهرة. على الرغم من المخاطر الكبيرة ، تم تنفيذ الفكرة. وفي أكتوبر ، دخل معسكر مدرع ، تم أخذه من مصنع ماريوبول ، الخدمة. تم تجميعه في 54 يومًا فقط. وفقًا لمعايير ما قبل الحرب ، استغرق هذا عامًا.
حصل مصنع نوفو تاجيل على المعسكر من لينينغراد. بدأت الاستعدادات لدخوله في يوليو ، وكان من المفترض في البداية أنه سيتم تثبيته على موقع الضمادة. تم تفكيك معسكر الضمادات ، لكن اتضح أن المخزون القديم لم يكن كافياً لتركيب المعسكر المدرع وكان لابد من وضعه في مكان آخر. أجبرت الحرب على فعل ما كان يعتبر مستحيلًا حتى وقت قريب: قبل عام واحد فقط ، حققت محاولات تنفيذ الإنشاءات الصناعية بطريقة متكاملة "عالية السرعة" في نيجني تاجيل نجاحًا جزئيًا في أحسن الأحوال ، وفي صيف عام 1941 حققت أكثر من كانت عملية البناء المعقدة مثالية تقريبًا. في 10 سبتمبر ، تم درفلة صفائح تاجيل الفولاذية الأولى قبل شهر من الموعد المحدد. في المجموع ، بحلول نهاية العام ، تم الحصول على 13650 طنًا من الصفائح المعدنية ، بما في ذلك حوالي 60 في المائة من الدروع (تم اختبار الطاحونة على الفولاذ الكربوني ، وفي أكتوبر - ديسمبر ، تم لف الصلب الكربوني بنقص سبائك الدروع). نتيجة لذلك ، في يناير 1942 ، تجاوز الإنتاج الشهري للصفائح المدرعة في مصانع الأورال ستة أشهر في الاتحاد السوفيتي قبل الحرب بأكمله.
وقعت أحداث لا تقل إثارة للدهشة في مؤسسات أخرى غير معروفة. خلال الحرب ، كان مصنع Zlatoust للمعادن أدنى من Magnitogorsk Combine من حيث حجم الصهر والفولاذ المدلفن ، لكنه تجاوزه بشكل كبير في مزيج منتجاته - حيث تم إنتاج حوالي 300 درجة من السبائك والفولاذ الكربوني هنا. بدون الإمدادات من Zlatoust ، كان إنتاج العديد من أنواع الأسلحة ، وخاصة محركات الدبابات ، قد توقف.
أثبتت مصانع الأورال القديمة أنها لا غنى عنها في إنتاج دفعات صغيرة من الفولاذ عالي الجودة بشكل خاص. على سبيل المثال ، تم استثمار معادن من Serov Metallurgical ، الشركة المصنعة الرئيسية للمنتجات المدرفلة المعايرة ، في كل دبابة سوفيتية. تحول مصنع نيجنسالدا إلى صهر الحديد والصلب. يمكن أن تستمر هذه القائمة إلى ما لا نهاية - خلال سنوات الحرب ، أينما كانت هناك قبة واحدة على الأقل ، تم صهر المعدن المستخدم في صنع الأسلحة.
هناك قصة غريبة تتعلق بتدفقات اللحام الآلي. قبل الحرب وفي بدايتها ، تم صهرها في إحدى مؤسسات دونباس ، وبعد احتلالها توقفت الإمدادات المركزية تمامًا. في نهاية عام 1941 ، بدأ موظفو معهد اللحام الكهربائي التابع لأكاديمية العلوم في جمهورية أوكرانيا الاشتراكية السوفياتية في البحث عن مواد بديلة متوفرة في جبال الأورال في حالة قابلة للاستخدام إلى حد ما. ووجدوها - في شكل خبث أفران صهر من مصنع أشينسكي المعدني.كانت هناك حاجة إلى تحسينات صغيرة فقط: قامت أفران الصهر بإثراء خبثها بالمنغنيز وبالتالي تحويلها إلى تدفق مناسب تمامًا. تم إحضار المعدات اللازمة للاختبار من نيجني تاجيل مباشرة إلى آشا.
أمثلة على التعاون المحلي بين مصانع الخزانات والمعادن دلالة للغاية. قبل إطلاق منشآتها الخاصة ، تم إجراء المعالجة الحرارية لأجزاء الخزان في مصنع Ural Tank رقم 183 في مصنع نيجني تاجيل للمعادن.
تم تسهيل العمل الناجح لعمال مسبك UTZ إلى حد كبير بمساعدة مصنع Nizhniy Tagil fireclay المجاور ، والذي أنشأ إنتاج سدادات الصوان المقاومة للحرارة عالية الجودة. هذا جعل من الممكن إجراء صب خالي من المتاعب لذوبان الفولاذ المدرع الثقيل من أجل الصب على شكل.
في 1942-1945 ، كانت أفران الموقد المكشوفة في UTZ تعمل بشكل أساسي على فرن فحم الكوك وغاز أفران الصهر من مصانع نوفو تاجيل ميتالورجيكال ونيزني تاجيل كوك. خط أنابيب الغاز يعمل منذ فبراير 1942. لم توفر محطة توليد الغاز الخاصة بالمحطة رقم 183 أكثر من 40 بالمائة من الاحتياجات.
في بعض الأحيان ، كانت نصيحة بسيطة كافية لحل مشكلة ما. ساعدت المعلومات الواردة من علماء المعادن المحليين حول منجم صغير للمنغنيز تم تطويره في سبعينيات القرن التاسع عشر على البقاء على قيد الحياة قبل عدة أسابيع من بدء تسليم المنغنيز الحديدي دون إيقاف صب مسارات الخزان.
مثال آخر: مع زيادة إنتاج الفولاذ المدرع ، لم يعد بإمكان المحل المفتوح مواكبة صهر المعدن لرؤوس القنابل الجوية. لم يكن من الممكن الحصول عليها من الخارج. استذكر المدير Yu. E. رؤوس القنبلة. قال: لا أستطيع المساعدة في الفولاذ ، لكن بالنصيحة سأساعد. وعندما أتيت إلى مصنعه ، أظهر لي محول بيسمير بوزن طن ونصف طن مع النفخ المتوسط. أعطاني الرسومات وقال إنه يعرف أن لدينا مسبكًا ميكانيكيًا جيدًا للحديد ، وستلحم المحولات الخاصة بك . هذه هي الطريقة التي ظهر بها طلب المصنع في 8 سبتمبر 1942 على المنظمة في متجر Griffin wheel في قسم Bessemer المكون من ثلاثة محولات صغيرة (طن ونصف من المعدن لكل منهما). بحلول 25 سبتمبر ، تم إعداد المشروع من قبل قسم التصميم والتكنولوجيا لإدارة البناء الرأسمالي ، وسرعان ما قام المتخصصون في قسم الميكانيكي الرئيسي بلحام المحولات والمراجل - خزانات تخزين الحديد السائل. تم إجراء الاختبار التجريبي لقسم Bessemer وصب مجموعة تجريبية من خمسة أسماء للأجزاء في مطلع أكتوبر ونوفمبر 1942. بدأ الإنتاج المسلسل في نهاية نوفمبر.
في نهاية الموضوع: عمل تعاون علماء المعادن وبناة الدبابات في زمن الحرب في كلا الاتجاهين. شارك القائمون على تركيب مصنع Ural Tank في تشغيل العديد من الوحدات الجديدة في Novo-Tagil Metallurgical Plant. في مايو 1944 ، تم تصنيع عدد كبير من ألواح التبطين لإصلاح الفرن العالي في ورشة صب الأبراج المدرعة.
لكن المساعد الرئيسي لعلماء المعادن كان ، بالطبع ، مصنع الأورال لبناء الآلات الثقيلة. تمت تعبئة كتب طلبات UZTM للأعوام 1942-1945 حرفيًا بالوثائق المتعلقة بإنتاج قطع الغيار والأجهزة للأغراض المعدنية - سواء لتلبية احتياجات صناعة الخزانات أو لشركات مفوضية الشعب للمعادن الحديدية. في خريف عام 1942 ، تم ترميم قسم خاص لإنتاج معدات مصانع التعدين رسميًا في UZTM. حصلت على رمز "القسم 15" وكانت تابعة لنائب مدير محلات المشتريات وإنتاج البدن.
النجاح عند تقاطع الصناعات
أدى تعاون علماء المعادن وبناة الخزانات إلى إنشاء عدد من التقنيات التي يمكن ، دون مبالغة ، أن تسمى اختراقات علمية وتقنية حقيقية.
بعد صهر الفولاذ المدرع وتدحرجته إلى صفائح ، نقل علماء المعادن منتجاتهم إلى إنتاج بدن مدرع. هنا تم قطع المعدن وفقًا للقالب إلى الأجزاء المقابلة. في إنتاج "أربعة وثلاثين" ، تم تسليم الكثير من المتاعب من خلال جزأين من الهيكل: المصدات (الجانب المائل من الجانب) واللوحة الجانبية الرأسية. كان كلاهما طويلًا ، حتى في شرائط العرض مع قطع مائلة على طول الحواف.
اقترحت الفكرة بشكل طبيعي أن تدحرج شريط قياس يساوي عرضه للأجزاء النهائية. تمت صياغته لأول مرة بواسطة السيارات المدرعة لمصنع ماريوبول في صيف عام 1941. للدحرجة التجريبية ، اخترنا طاحونة ألواح في Zaporizhstal ، حيث تم إرسال مستويين من سبائك الدروع. ولكن بعد ذلك لم يكن لديهم الوقت للانخراط في العمل: استولت القوات الألمانية المتقدمة على كل من المراتب وزابوروجي نفسها.
في مطلع عام 1941-1942 ، أثناء الإخلاء وتطوير إنتاج الدروع في المصانع الجديدة ، لم يكن هناك ما يكفي من الشريط. ومع ذلك ، في مايو 1942 ، تلقت مفوضية الشعب لعلم المعادن الحديدية مرة أخرى أمرًا بتأجيرها لخزانات T-34 و KV. اتضح أن المهمة صعبة: يجب ألا تتجاوز التفاوتات في العرض -2 / + 5 ملم ، وشكل الهلال (الانحناء) للطول الإجمالي للجزء 5 ملم. لم يُسمح بالشقوق وغروب الشمس والتشقق عند الحواف بحيث يمكن إجراء اللحام دون استخدام الآلات أو القطع باللهب.
بدأ العمل التجريبي في وقت واحد في ورش الدرفلة في مصانع Magnitogorsk و Kuznetsk المعدنية ، في البداية دون أي إنجازات معينة. سرعان ما تم التخلي عن استئجار أجزاء لخزانات KV ، لكن T-34 نجحت أخيرًا. يعتبر فريق المؤلفين المكون من رئيس قسم المعادن في NII-48 G. طريقة المتداول "على الحافة". في يناير 1943 ، تم إصدار 280 شريطًا ، في فبراير - 486 ، في مارس - 1636 قطعة. في أبريل ، بعد كل الاختبارات المطلوبة ، بدأ تطوير الإنتاج الإجمالي لشرائط القياس لبطانات قوس العجلة لخزانات T-34. في البداية ، تم توريدها إلى UZTM ومصنع Ural Tank ، ثم إلى المصانع الأخرى - الشركات المصنعة لخزانات T-34. انخفضت الخردة ، التي كانت في الأصل 9.2 في المائة ، إلى 2.5 في المائة بحلول أكتوبر 1943 ، واستخدمت الشرائح المتدنية الجودة لصنع أجزاء أصغر.
يتم تقديم تقييم كامل ودقيق للتكنولوجيا الجديدة من خلال التقرير المقابل لـ TsNII-48 بتاريخ 25 ديسمبر 1943: "تم تطوير واختبار طريقة جديدة بشكل أساسي لتدحرج شريط مدرع عريض" على الحافة "وإدخالها في إجمالي الإنتاج ، والتي كانت تعتبر غير مجدية حتى وقت قريب في الاتحاد السوفياتي وفي الخارج. أتاح الحصول على شريط معاير (مُقاس) بعرض الجزء النهائي من الهيكل المدرع لخزان T-34 لمصانع NKTP اعتماد تقنية جديدة عالية الأداء لتصنيع الأجزاء المدرعة دون قطع الحواف الطولية. بفضل تطبيق الطريقة الجديدة على أحد الأجزاء الرئيسية المدرعة من دبابة T-34 (المصدات) ، تم توفير وقت كبير جدًا (حوالي 36 ٪) عند الاستغناء عنها. تم تحقيق وفورات في 8C Armor steel بنسبة تصل إلى 15 بالمائة وتوفير أكسجين قدره 15000 متر مكعب لكل 1000 هيكل ".
بحلول نهاية عام 1943 ، تم إتقان دحرجة شريط قياس لجزء آخر من هيكل T-34 - الجزء الرأسي من الجانب. يبقى فقط أن نضيف أن مؤلفي هذا الاختراع حصلوا على جائزة ستالين لعام 1943.
في نفس عام 1943 ، من خلال الجهود المشتركة لمختبر المعهد الأوكراني للمعادن (برئاسة PA Aleksandrov) والعاملين في Kuznetsk Metallurgical Combine و Ural Tank Plant ، تم تطوير ملف تعريف دوري خاص مدلفن وإتقانه في الإنتاج من أجل الشراء للكتلة والأجزاء الحرجة من "أربعة وثلاثين" - موازن المحاور.تم استلام الدفعة التجريبية الأولى من الملف الشخصي الدوري في KMK في ديسمبر ، في بداية عام 1944 بدأ الإنتاج التسلسلي. بحلول أكتوبر ، تحول مصنع Ural Tank بالكامل إلى تصنيع محاور الموازن من فراغ جديد ، في نهاية العام انضم إليه UZTM. ونتيجة لذلك ، زادت إنتاجية مطارق الحدادة بنسبة 63 بالمائة وانخفض عدد الكسور الجزئية.
تم تسهيل العمل الناجح لبناة الخزانات إلى حد كبير من خلال المخزون الدارجة لمصنع الضمادات في مصنع Novo-Tagil Metallurgical. بدءًا من ربيع عام 1942 ، قاموا بتزويد أحزمة الكتف الملفوفة ببدلات تصنيع مخفضة ، وفي عام 1943 تم تخفيض البدلات مرة أخرى. بالاقتران مع أداة القطع الجديدة ، أتاح ذلك إمكانية تجريد أحزمة الكتف التي تستغرق وقتًا طويلاً بشكل صارم في الموعد المحدد ودون إجهاد كبير. حالة نادرة: اعتبر مفوض الشعب في صناعة الخزانات V. A. Malyshev ، في أمره الصادر في 28 سبتمبر 1943 ، أنه من الضروري التعبير عن امتنانه الخاص لعلماء المعادن في تاجيل.
وأخيرًا ، المثال الأخير: في عام 1943 ، بدأ تصنيع حواف خزانات الدعم T-34 ، أولاً في مصنع Chelyabinsk Kirov ، ثم في المؤسسات الأخرى ، من منتجات ملفوفة خاصة. لوحظ هذا النجاح أيضًا بترتيب V. A. Malyshev.
ويبقى أن نضيف أن المتخصصين في شركة "كرايسلر" الأمريكية ، بعد أن درسوا دبابة T-34-85 التي تم الاستيلاء عليها في كوريا ، لاحظوا بشكل خاص إتقان الفراغات الفولاذية التي صنعت منها المركبة القتالية. وكذلك حقيقة أنها غالبًا ما كانت تفوق عددًا من منتجات الشركات المعدنية الأمريكية.