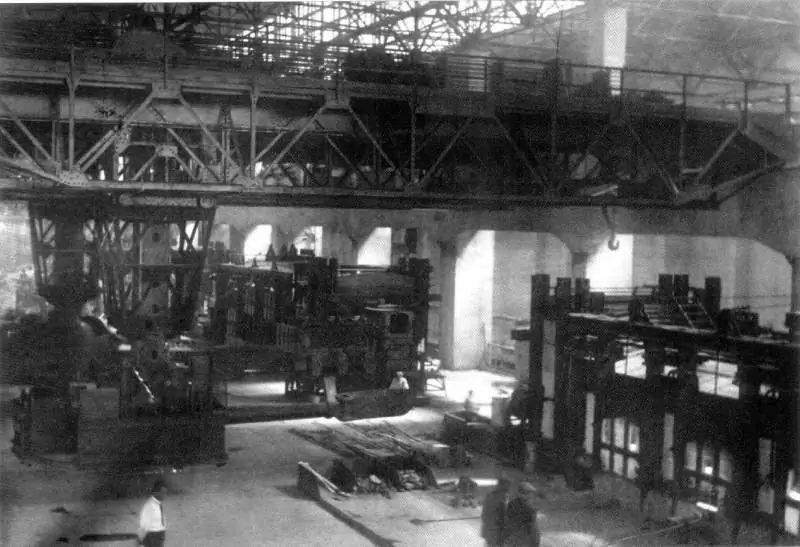
المورد الاستراتيجي
من الصعب المبالغة في تقدير إنتاج الصلب عالي الجودة للمجمع الصناعي العسكري في ظروف الحرب. وهذا من أهم عوامل نجاح الجيوش في ساحة المعركة.
كما تعلم ، كان علماء المعادن في Krupp من بين أول من تعلم كيفية إنتاج فولاذ عالي الجودة يستخدم في صناعة الأسلحة.
تبنى الألمان عملية تصنيع توماس في نهاية القرن التاسع عشر. أتاحت طريقة صهر الفولاذ هذه إزالة شوائب الفوسفور من الركاز ، مما أدى تلقائيًا إلى زيادة جودة المنتج. غالبًا ما ضمنت الدروع والأسلحة الفولاذية عالية الجودة خلال الحرب العالمية الأولى تفوق الألمان في ساحة المعركة.
لتنظيم مثل هذا الإنتاج ، كانت هناك حاجة إلى مواد حرارية جديدة ، والتي تبطن الأسطح الداخلية للأفران. استخدم الألمان في وقتهم أحدث حراريات المغنسيت ، وتحمل درجات حرارة تزيد عن 2000 درجة. تعتمد هذه المواد ذات المقاومة العالية على أكاسيد المغنيسيوم مع مواد مضافة صغيرة من أكاسيد الألومنيوم.
في بداية القرن العشرين ، كانت البلدان التي لديها تقنيات للإنتاج الضخم لحراريات المغنسيوم قادرة على إنتاج دروع وبنادق براميل عالية الجودة. يمكن مقارنة هذا بميزة استراتيجية.
كانت أقل من حيث مقاومة الحريق ما يسمى بالمواد شديدة المقاومة للحرارة والتي تتحمل درجات حرارة من 1750 إلى 1950 درجة. هذه هي حراريات الدولوميت والألومينا العالية. يمكن أن تتحمل المواد المقاومة للحرارة فيريكلاي وشبه الحمضية والكوارتز والدينا درجات حرارة من 1610 إلى 1750 درجة.
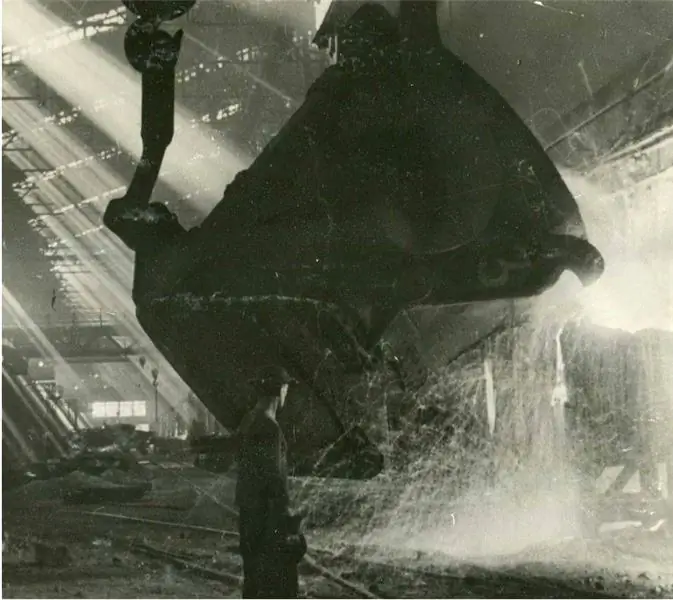
بالمناسبة ، ظهرت تقنيات ومواقع إنتاج حراريات المغنسيوم لأول مرة في روسيا في عام 1900.
حصل الطوب المقاوم للحرارة من المغنسيت ساتكا في عام 1905 على ميدالية ذهبية في المعرض الصناعي العالمي في لييج. تم إنتاجه بالقرب من تشيليابينسك في مدينة ساتكا ، حيث توجد رواسب مغنسيت فريدة من نوعها.
كان معدن البريكلاز ، الذي صنعت منه الحراريات في المصنع ، ذا جودة عالية ولم يتطلب تخصيبًا إضافيًا. نتيجة لذلك ، كان صهر المغنسيت من ساتكا متفوقًا على نظرائه من اليونان والنمسا.
سد الفجوة
على الرغم من طوب المغنسيت عالي الجودة من Satka ، حتى الثلاثينيات ، كانت الحراريات الرئيسية لعلماء المعادن السوفييت هي مواد الديناص من الطين. بطبيعة الحال ، لم ينجح الحصول على درجة حرارة عالية لصهر الفولاذ المستخدم في صناعة الأسلحة - فقد انهارت البطانة الداخلية لأفران الموقد المفتوحة وتطلبت إصلاحات غير عادية.
لم يكن هناك ما يكفي من لبنة ساتكا ، وفي فترة ما بعد الثورة ، فقدت تقنيات الإنتاج الرئيسية.
في الوقت نفسه ، ذهب الأوروبيون إلى الأمام - على سبيل المثال ، تميز المغنسيت النمساوي Radex بمقاومة ممتازة للحريق.
اشترى الاتحاد السوفيتي هذه المواد. لكن كان من المستحيل الحصول على نظير بدون سر إنتاج. تم تناول هذه المشكلة من قبل أحد خريجي جامعة موسكو التقنية الحكومية. م. بومان أليكسي بتروفيتش بانارين. في مصنع Magnet (المعروف سابقًا باسم Satka Combine) في عام 1933 ، ترأس مختبر النبات المركزي. وبعد خمس سنوات ، أطلق الإنتاج الضخم لكروميت البريكلاز أو حراريات الكروم المغنسيوم لأفران الموقد المفتوحة.
في مصنع Zlatoust Metallurgical و Moscow Hammer and Sickle ، حلت حراريات Panarin محل الديناص القديمة.
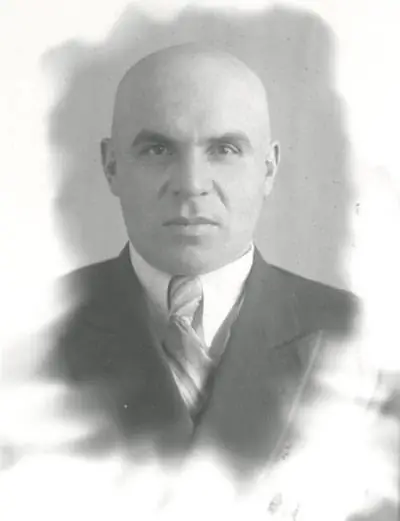
تتكون التكنولوجيا ، التي تم تطويرها في مختبر "Magnezit" لعدة سنوات ، من تركيبة خاصة وحجم الجسيمات.
في السابق ، أنتج المصنع طوب الكروم المغنسيت التقليدي ، الذي يتكون من خام الحديد المغنسيت والكروم ، بنسبة 50/50. السر الذي كشفته مجموعة بانارين كان كالتالي:
إذا تمت إضافة خام الكروميت في حبيبات حبيبية خشنة ذات محتوى أدنى من الكسور أقل من 0.5 مم إلى شحنة مغنسيت عادية ، فعندئذٍ حتى مع إضافة 10٪ من هذا الخام ، فإن الاستقرار الحراري للطوب يزيد بشكل حاد.
مع زيادة إضافة خام الكروميت لقياس الحبيبات الخشنة ، ينمو ثبات الطوب ويصل إلى الحد الأقصى عند نسبة معينة من المكونات.
تم أخذ الكروميت للحرارة الجديدة في منجم سارانوفسكوي ، واستمر تعدين البريكلاز في ساتكا.
للمقارنة ، صمدت طوب المغنسيت العادي "ما قبل الثورة" في درجات حرارة تقل بمقدار 5-6 مرات عن حداثة بانارين.
في مصنع كيروفوغراد لصهر النحاس ، صمد الكروم والمغنسيت المقاوم للصهر في سطح فرن عاكس صامدًا لدرجات حرارة تصل إلى 1550 درجة لمدة 151 يومًا. في السابق ، كان لابد من تغيير الحراريات في هذه الأفران كل 20-30 يومًا.
بحلول عام 1941 ، تم إتقان إنتاج الحراريات على نطاق واسع ، مما جعل من الممكن استخدام المواد في أفران كبيرة لصنع الفولاذ في درجات حرارة تصل إلى 1800 درجة. تم تقديم مساهمة مهمة في ذلك من قبل المدير الفني لـ "Magnezit" Alexander Frenkel ، الذي طور طريقة جديدة لتثبيت المواد المقاومة للحرارة على أسطح الأفران.
حراريات للنصر
في نهاية عام 1941 ، أنجز علماء المعادن في Magnitka ما لم يكن من الممكن تصوره سابقًا - لأول مرة في التاريخ أتقنوا صهر الفولاذ المدرع لدبابات T-34 في أفران الموقد الثقيلة الرئيسية.
كان المورد الرئيسي للحراريات لهذه العملية الهامة هو Satka "Magnezit". لا داعي للحديث عن صعوبات زمن الحرب ، عندما تم استدعاء ثلث عمال المصانع إلى الجبهة ، وطالبت الدولة بإفراط في تنفيذ الخطة. ومع ذلك ، كان المصنع يقوم بعمله ، وبانارين في عام 1943
"لإتقان إنتاج منتجات عالية المقاومة للحرارة من المواد الخام المحلية للمعادن الحديدية"
حصل على جائزة ستالين.
في عام 1944 ، سيطور باحث المعادن هذا تقنية لإنتاج مسحوق المغنسيوم عالي الجودة "إكسترا". تم استخدام هذا المنتج شبه النهائي لإعداد مادة مقاومة للحرارة مضغوطة تستخدم في الإنتاج المهم بشكل خاص للفولاذ المدرع في الأفران الكهربائية. وصلت درجة الحرارة القصوى لمثل هذه الحراريات إلى 2000 درجة.
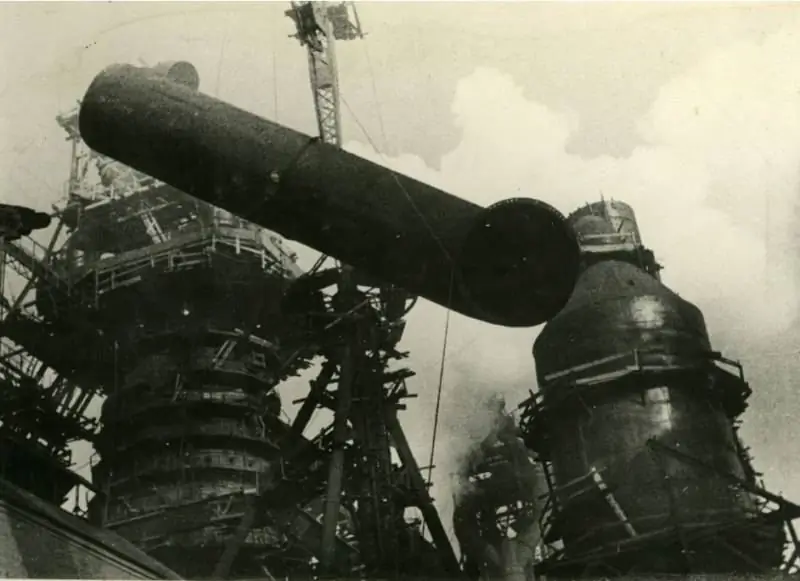
لكن لا ينبغي للمرء أن يفترض أن مثال مصنع Magnezit الناجح عمومًا امتد ليشمل الصناعة الحرارية بأكملها في الاتحاد السوفيتي.
تطور وضع صعب بشكل خاص في جبال الأورال ، حيث تم إخلاء جميع مباني الدبابات في البلاد تقريبًا في 1941-1942.
تم إعادة توجيه مصانع Magnitogorsk و Novotagilsk للمعادن لإنتاج الدروع ، وتوريد المنتجات إلى مصنع Sverdlovsk Uralmash و Chelyabinsk "Tankograd" و Nizhny Tagil رقم 183. في الوقت نفسه ، كان للمصانع المعدنية إنتاجها الخاص من الحراريات من المواد الخام المحلية.
على سبيل المثال ، في Magnitka ، أنتج مصنع dinas-chamotte 65-70 ألف طن من الطوب سنويًا. لم يكن هذا كافيًا حتى لاحتياجاتهم الخاصة ، ناهيك عن الإمدادات للمؤسسات الأخرى.
نشأت الصعوبات الأولى عندما بدأت مصانع الخزانات في بناء أفران التدفئة والحرارة الخاصة بها. كان لدى علم الأورال بالفعل ما يكفي من الحراريات ، ومن ثم تطلب إنتاج بدن مصانع الخزانات مواد عالية الجودة لبطانة الأفران.
لم يكن هناك حديث عن أي مواد حرارية للكرومومغنيزيت هنا - كانت هذه المادة قليلة العرض ، وحتى تم تصديرها مقابل American Lend-Lease. على الأقل هذا مذكور في عدد من المصادر. كتب مؤرخو الأورال أن الكرومومغنسيت الباهظ الثمن لبانارين يمكن أن يسافر إلى الخارج مقابل سبائك حديدية نادرة لدروع الدبابات. لكن لا يوجد دليل مباشر على ذلك حتى الآن.
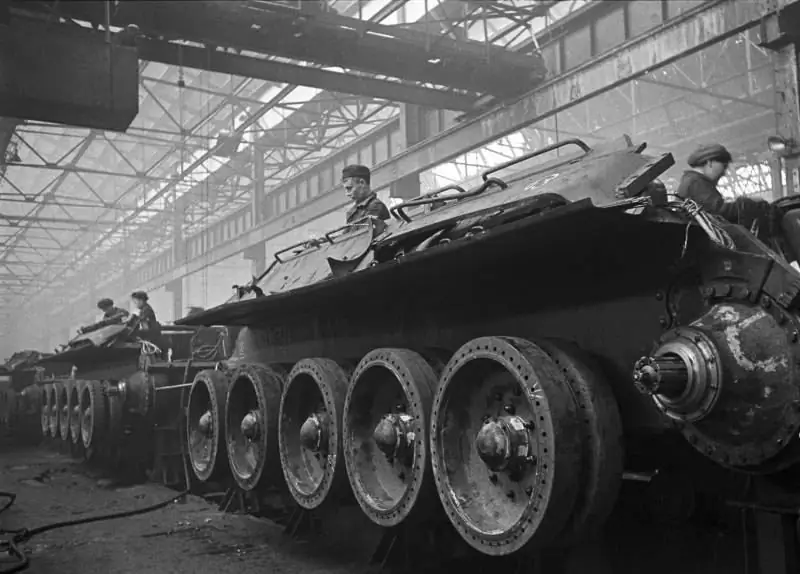
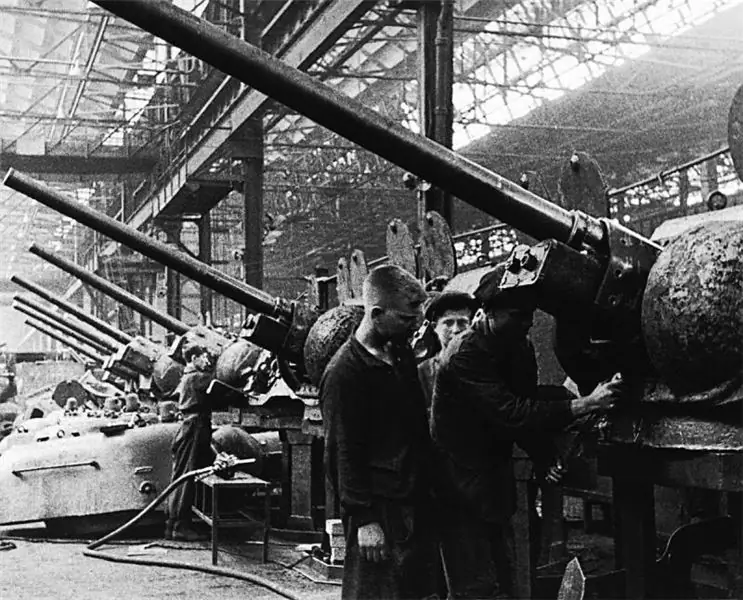
اعتمدت مصانع الخزانات في الغالب على مادة صهر الديناس التي ينتجها مصنع برفورالسك. ولكن ، أولاً ، تم إنتاجه فقط 12 ألف طن شهريًا ، وثانيًا ، أخذ علماء المعادن نصيب الأسد.
سار توسع الإنتاج في مصنع Pervouralsk ببطء شديد. وبحلول منتصف عام 1942 ، ظهرت 4 أفران جديدة فقط. أما البقية فلم تكن جاهزة ، أو كانت موجودة بشكل عام فقط في المشاريع.
غالبًا ما كانت الحراريات الخاصة بأفران الموقد المفتوحة لمصانع الخزانات ذات جودة رديئة ، وليست كاملة وفي الوقت الخطأ. فقط لإصلاح أفران Uralmash في الربع الرابع من عام 1942 ، كانت هناك حاجة إلى 1035 طنًا من الطوب المقاوم للحريق ، وتم استلام حوالي 827 طنًا فقط.
في عام 1943 ، توقف متجر الموقد المفتوح في أورالماش بشكل عام تقريبًا بسبب نقص الحراريات للإصلاح.
تركت جودة الحراريات التي تم توفيرها طوال الحرب الكثير مما هو مرغوب فيه. إذا كان لبنة ديناس في فرن الموقد المفتوح ، في ظل الظروف العادية ، يمكن أن تتحمل 400 درجة حرارة ، فلن تتجاوز 135 درجة حرارة في زمن الحرب. وبحلول مارس 1943 ، انخفضت هذه المعلمة إلى 30-40 درجة حرارة.
يوضح هذا الموقف بوضوح كيف يمكن أن يؤدي عدم وجود مورد واحد (في هذه الحالة ، مقاوم للحرارة) إلى إبطاء عمل صناعة الدفاع بأكملها بشكل خطير. كما كتب مرشح العلوم التاريخية نيكيتا ميلنيكوف في أعماله ، في مارس 1943 ، لا تزال ثلاثة أفران مفتوحة في أورالماش متوقفة ونفذت دورة كاملة من أعمال الإصلاح. وقد استهلكت 2346 طناً من الدينا و 580 طناً من الشاموت و 86 طناً من المغنسيت الشحيح.
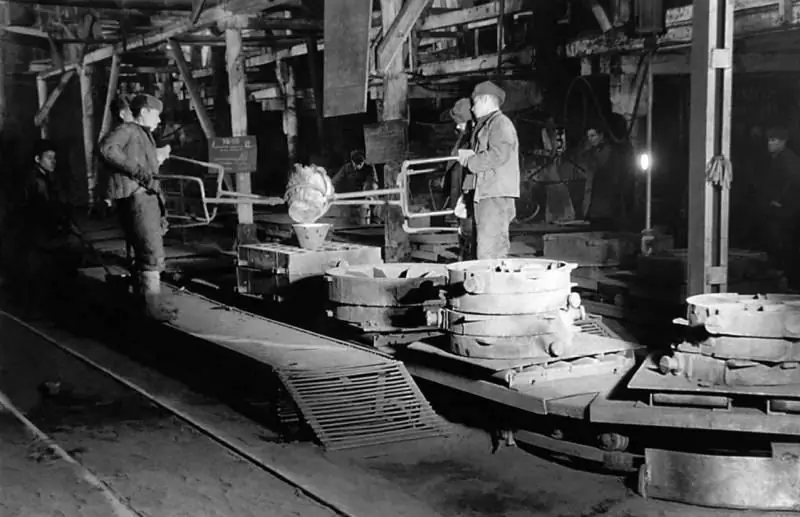
بحلول منتصف عام 1942 ، في مصنع الخزانات رقم 183 ، كان الوضع يتطور بطريقة مماثلة - تأخر إنتاج الصلب عن التجميع الميكانيكي. وكان علينا "استيراد" هياكل T-34 من Uralmash.
كان أحد الأسباب هو عدم وجود الحراريات لإصلاح أفران الموقد المفتوحة ، والتي كانت تعمل في ربيع عام 1942 بأقصى طاقتها. ونتيجة لذلك ، تم تشغيل 2 فقط من أصل 6 أفران مفتوحة في الخريف ، ولم تتم استعادة أحجام الصهر إلا في النصف الثاني من عام 1943.
يوضح الوضع مع الحراريات في هيكل مجمع الدفاع السوفيتي خلال الحرب الوطنية العظمى بوضوح مدى تعقيد الوضع في الجزء الخلفي من البلاد.
النقص المزمن ، بشكل عام ، ليس أكثر المنتجات عالية التقنية أثر بشكل مباشر على وتيرة إنتاج المركبات المدرعة.